Electro-optical or electromechanical structural element or sliding element
A photoelectric component, electromechanical technology, applied in the direction of electrical components, contact parts, circuits, etc., can solve the problems of rough surface, unsatisfactory optical performance or mechanical performance, etc., achieve the effect of improving friction coefficient, improving functionality and reducing usage
- Summary
- Abstract
- Description
- Claims
- Application Information
AI Technical Summary
Problems solved by technology
Method used
Image
Examples
Embodiment Construction
[0028] figure 1 The rolling process on the surface of the metal substrate 1 is schematically shown. The surface is configured as an open structure. In order to form the open structure, individual depressions 12 are rolled on the undeformed surface 11 of the metal substrate 1 which still has a smooth appearance. Arranged on the surface of the rolling bodies 22 of the roller 2 used are spherical caps 21 which penetrate the surface of the metal base plate 1 . For example, the spherical caps 21 are of the same size so that they produce the same negative structure on the substrate surface. As an alternative, however, the structural dimensions of the roller surface can be very different, and other shapes, for example conical or cylindrical, are also conceivable. In any case, this is the fine structure comprising the almost smooth undeformed raw background of the initial surface formed by rolling from the substrate surface.
[0029] figure 2 Shown is a rolled substrate surface ...
PUM
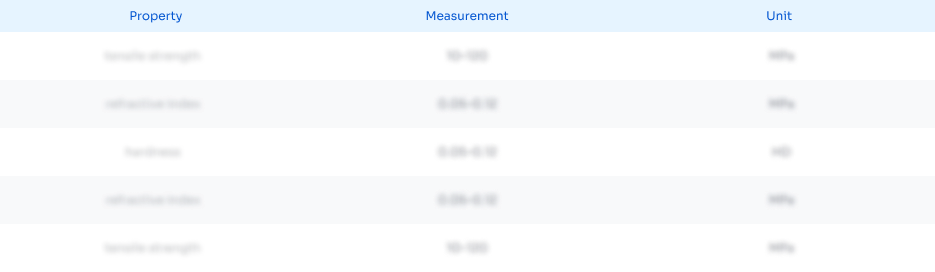
Abstract
Description
Claims
Application Information

- R&D
- Intellectual Property
- Life Sciences
- Materials
- Tech Scout
- Unparalleled Data Quality
- Higher Quality Content
- 60% Fewer Hallucinations
Browse by: Latest US Patents, China's latest patents, Technical Efficacy Thesaurus, Application Domain, Technology Topic, Popular Technical Reports.
© 2025 PatSnap. All rights reserved.Legal|Privacy policy|Modern Slavery Act Transparency Statement|Sitemap|About US| Contact US: help@patsnap.com