Method for utilizing residues of catalyst production
A catalyst and waste residue technology, applied in the field of waste residue utilization, can solve the problems of poor hydrothermal stability, low heavy oil cracking capacity, poor coke and dry gas selectivity, etc., and achieves good hydrothermal stability, high yield, The effect of high activity stability
- Summary
- Abstract
- Description
- Claims
- Application Information
AI Technical Summary
Problems solved by technology
Method used
Image
Examples
preparation example Construction
[0025] In the preparation method of active carrier provided by the invention, ammonium salt or alkali metal salt is used to exchange in step (3), and the conditions of exchange include: the temperature of exchange is 30~80 ℃, the exchange time is 0.2~2 hours, waste residue (on a dry basis The weight ratio of ammonium salt (or alkali metal salt) to ammonium salt (or alkali metal salt) is 10-20:1, the pH value is 2-4, and the weight ratio of water and waste residue in the exchange solution is 5-20:1. The calcination time in step (3) is 1-2 hours; the calcination temperature is preferably 500-700°C. The ammonium salt is preferably ammonium chloride and / or ammonium nitrate, and the alkali metal salt is preferably sodium chloride or sodium nitrate. The washing is an existing method, such as washing with deionized water, usually according to the waste residue solid after exchange: water=1:5~20 ratio washing, to remove the free heteroions exchanged, the temperature can be normal temp...
Embodiment approach
[0027]The preparation method of the active carrier provided by the invention, a specific embodiment, comprises:
[0028] (1) drying the waste catalyst residue at 100-150° C. for 1-5 hours;
[0029] (2) The material obtained in step (1) is contacted with ammonium salt for ion exchange, and then washed, the exchange temperature is 30~80°C, and the exchange time is 0.2~2 hours. The weight ratio is 5-10:1, and the pH is 2.0-3.0.
[0030] (3) Roasting the material obtained in step (2) for 1 to 2 hours at 500 to 700°C, then washing and filtering, the exchange temperature is 30 to 80°C, and the exchange time is 0.2 to 2 hours. Waste residue (on a dry basis) and The weight ratio of the ammonium salt is 10-20:1, and the pH is 2.0-4.0.
[0031] (4) mixing the material obtained in step (3) with wet or dry molecular sieve waste residue and water for beating, then filtering and drying at 100-150°C for 2-5 hours, and then roasting, the roasting temperature is 500-700°C, The roasting time...
Embodiment 1
[0034] Wet catalyst waste residue, obtained from Sinopec Catalyst Qilu Branch, has a solid content of 19.57% by weight, and the dry weight percentage is grouped as Na 2 O is 3.50%, MgO is 0.64%, Al 2 o 3 16.41%, SiO 2 36.96%, Re 2 o 3 6.00%, SO 3 18.13%, Fe 2 o 3 0.32%, K 2 O is 0.12%, Cl - 0.90%, CaO 14.20%, P 2 o 5 was 0.41%. The catalyst waste residue was dried at 150° C. for 2 hours, and 20 kg (dry basis) of the dried catalyst waste residue was taken with 100 kg deionized water and 4Kg NH 4 Cl mixed, adding hydrochloric acid to adjust the pH value to 3.0, beating at 60°C for 30min, filtering, washing the filter cake with 200Kg deionized water and roasting at 600°C for 1.5 hours, then the obtained roasted product was mixed with 100Kg deionized water and 2Kg NH 4 Mix with Cl, add hydrochloric acid to adjust the pH value to 3.0, beat at 60°C for 30 minutes, filter, wash the filter cake with 200Kg deionized water, and then dry at 140°C for 1.5 hours to obtain the ...
PUM
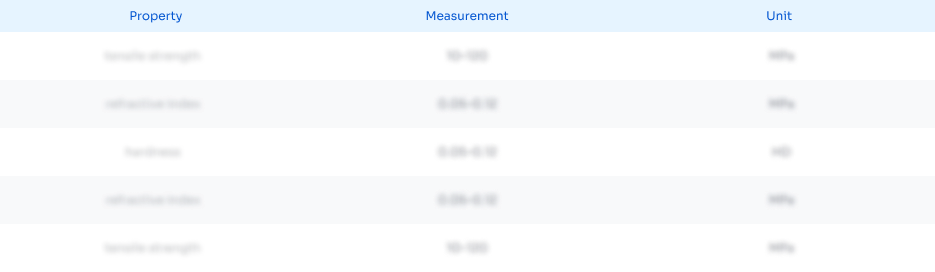
Abstract
Description
Claims
Application Information

- R&D
- Intellectual Property
- Life Sciences
- Materials
- Tech Scout
- Unparalleled Data Quality
- Higher Quality Content
- 60% Fewer Hallucinations
Browse by: Latest US Patents, China's latest patents, Technical Efficacy Thesaurus, Application Domain, Technology Topic, Popular Technical Reports.
© 2025 PatSnap. All rights reserved.Legal|Privacy policy|Modern Slavery Act Transparency Statement|Sitemap|About US| Contact US: help@patsnap.com