Twisted string drive-based finger of robot
A robot finger and rope-driven technology, which is applied in the direction of manipulators, chucks, manufacturing tools, etc., can solve the problems of high environmental cleanliness, positive and negative travel errors, and the size of robot fingers can not be too large, etc., to achieve small size and compact structure Effect
- Summary
- Abstract
- Description
- Claims
- Application Information
AI Technical Summary
Problems solved by technology
Method used
Image
Examples
Embodiment Construction
[0010] Such as figure 1 Shown, the invention is realized like this, and it comprises proximal finger section 1, middle finger section 2, last finger section 3, middle finger shaft 4, last finger shaft 5, coupling link 6, twisted rope rotating shaft 7, twisted rope 8, reply Spring 9 and motor 10, motor 10 is fixedly connected on the proximal finger segment 1, the middle finger segment 2 is connected on the proximal finger segment 1 through the middle finger shaft 4, the last finger segment 3 is connected on the middle finger segment 2 through the last finger shaft 5, and the last finger segment Section 3 and proximal finger section 1 are connected by coupling link 6, and one end of twisted rope 8 is connected on the rotating shaft of motor 10, and the other end is connected on the middle finger section 2 by twisted rope rotating shaft 7, and the two ends of return spring 9 are respectively connected on On the proximal finger section 1 and the middle finger section 2, the return...
PUM
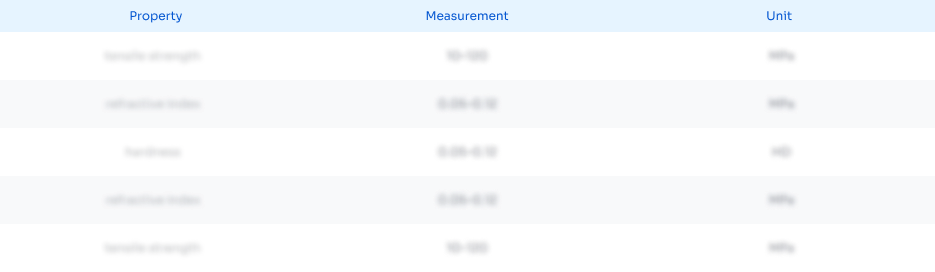
Abstract
Description
Claims
Application Information

- Generate Ideas
- Intellectual Property
- Life Sciences
- Materials
- Tech Scout
- Unparalleled Data Quality
- Higher Quality Content
- 60% Fewer Hallucinations
Browse by: Latest US Patents, China's latest patents, Technical Efficacy Thesaurus, Application Domain, Technology Topic, Popular Technical Reports.
© 2025 PatSnap. All rights reserved.Legal|Privacy policy|Modern Slavery Act Transparency Statement|Sitemap|About US| Contact US: help@patsnap.com