Device for carrying out hot stamping for multiple times on one impression roller
An embossing roller and the same technology, applied in the field of multiple bronzing devices, can solve problems such as waste of resources, and achieve the effects of reducing floor space, reducing costs, and improving bronzing efficiency.
- Summary
- Abstract
- Description
- Claims
- Application Information
AI Technical Summary
Problems solved by technology
Method used
Image
Examples
Embodiment Construction
[0018] Below in conjunction with accompanying drawing, the present invention is further described: as Figure 1~4 As shown in the above, the device for multiple stamping on the same embossing roller includes an embossing roller 6, at least a plurality of bronzing rollers with a front bronzing roller 3 and a rear bronzing roller 1 in the same embossing unit. Multiple hot stamping rollers are embossed by the same embossing roller 6; after the hot stamping roller, an ultrasonic micro humidifier 10 is arranged; Composed of a fixed layer 14; the heating layer 12 is provided with an electric heating member 16 corresponding to the bronzing plate 15, and the heat conducting layer 13 is provided with a heat conducting area 17 and a heat insulating area 18, and the heat conducting area 17 is located below the bronzing plate 15 , outside the heat conduction area 17 of the heat conduction layer is a heat insulation area 18, and regularly arranged honeycomb holes 19 are arranged on the fix...
PUM
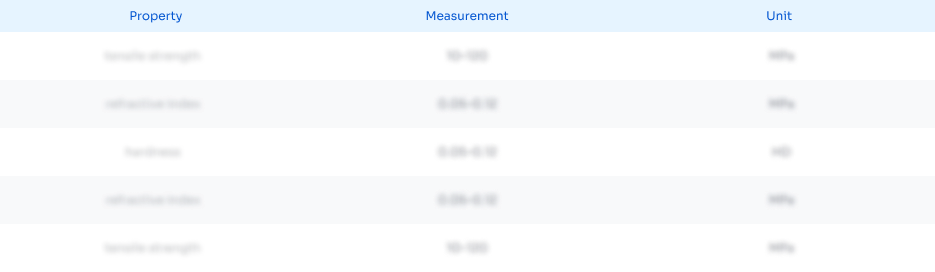
Abstract
Description
Claims
Application Information

- R&D Engineer
- R&D Manager
- IP Professional
- Industry Leading Data Capabilities
- Powerful AI technology
- Patent DNA Extraction
Browse by: Latest US Patents, China's latest patents, Technical Efficacy Thesaurus, Application Domain, Technology Topic, Popular Technical Reports.
© 2024 PatSnap. All rights reserved.Legal|Privacy policy|Modern Slavery Act Transparency Statement|Sitemap|About US| Contact US: help@patsnap.com