Dashboard beam frame laser welding system
A technology for automobile instrument panel and laser welding, applied in laser welding equipment, welding equipment, metal processing equipment, etc., can solve the problems of unguaranteed welding quality, complex system structure, low degree of automation, etc., and improve welding work efficiency , optimized welding process, and high degree of automation
- Summary
- Abstract
- Description
- Claims
- Application Information
AI Technical Summary
Problems solved by technology
Method used
Image
Examples
Embodiment Construction
[0018] The present invention will be further described below in conjunction with the accompanying drawings and embodiments.
[0019] As shown in the figure, the laser welding system for the beam skeleton of the automobile instrument panel in this embodiment includes an airtight welding room 1, a laser welding manipulator 2 arranged in the welding room 1, two rotary welding stations, an exhaust and dust removal system 3 and an automatic control system. System 4,
[0020] The rotary welding station includes a horizontally arranged station platform 5, a first servo motor (shown in the figure) fixedly connected to the station platform at the bottom of the station platform 5 and the rotating shaft is vertically upward, and is arranged on the station platform. The support beam 6 on the 5 and two welding tool installation platforms 7 symmetrically arranged on both sides of the rotation center of the station platform 5, one end of the welding work installation platform 7 and the secon...
PUM
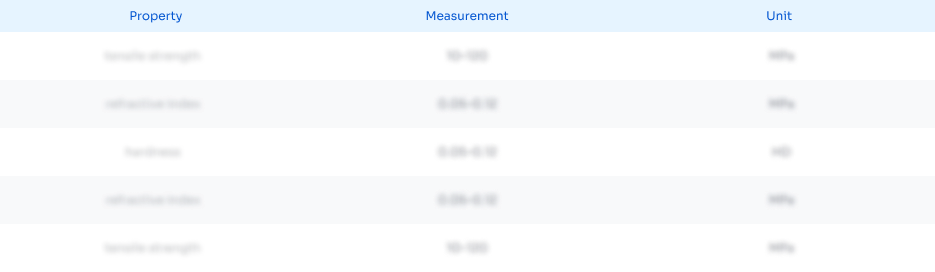
Abstract
Description
Claims
Application Information

- R&D Engineer
- R&D Manager
- IP Professional
- Industry Leading Data Capabilities
- Powerful AI technology
- Patent DNA Extraction
Browse by: Latest US Patents, China's latest patents, Technical Efficacy Thesaurus, Application Domain, Technology Topic, Popular Technical Reports.
© 2024 PatSnap. All rights reserved.Legal|Privacy policy|Modern Slavery Act Transparency Statement|Sitemap|About US| Contact US: help@patsnap.com