Large-scale centrifugal compressor impeller and machining forming method thereof
A centrifugal compressor and impeller technology, applied in metal processing equipment, mechanical equipment, manufacturing tools, etc., can solve the problem that the formed product deviates from the aerodynamic design requirements of the centrifugal compressor, the welding deformation is difficult to completely eliminate, and the surface finish of the die blade is poor, etc. To solve the problem, to achieve the excellent shape of the pneumatic flow channel, to eliminate the polishing weld bump, and to ensure the effect of the shape of the pneumatic flow channel
- Summary
- Abstract
- Description
- Claims
- Application Information
AI Technical Summary
Problems solved by technology
Method used
Image
Examples
Embodiment Construction
[0015] Below, combined with Figure 1-3 , taking a centrifugal impeller for a large centrifugal compressor as an example to illustrate the specific implementation of the present invention.
[0016] The impeller of the large centrifugal compressor described in one embodiment of the present invention is image 3 The shown centrifugal impeller 3 is welded by the disc side part 1 and the wheel cover side part 2 at the height of the half blade. Such as Figure 1-2 As shown, the wheel side part 1 is composed of the overall five-axis milling wheel disc and the wheel cover side half blade height, and the wheel cover side part 2 is composed of the overall five-axis milling wheel cover and the wheel cover side half height blade. Leaf composition.
[0017] Such as image 3 As shown, the forming process of the centrifugal impeller of the large centrifugal compressor described in this embodiment adopts the method of butt-welding the respective milled and shaped blades in the middle of ...
PUM
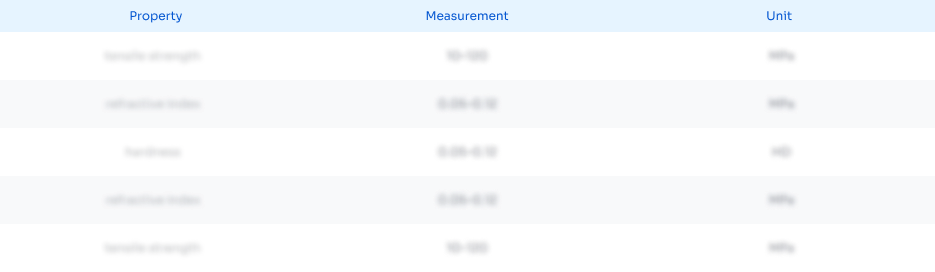
Abstract
Description
Claims
Application Information

- Generate Ideas
- Intellectual Property
- Life Sciences
- Materials
- Tech Scout
- Unparalleled Data Quality
- Higher Quality Content
- 60% Fewer Hallucinations
Browse by: Latest US Patents, China's latest patents, Technical Efficacy Thesaurus, Application Domain, Technology Topic, Popular Technical Reports.
© 2025 PatSnap. All rights reserved.Legal|Privacy policy|Modern Slavery Act Transparency Statement|Sitemap|About US| Contact US: help@patsnap.com