Meter pointer angle identification method based on image processing
An instrument pointer and image processing technology, which is applied in the field of image processing, can solve problems such as the large error of the instrument pointer frame difference method, and achieve the effects of eliminating detection deviations, intuitive image processing results, and improving performance
- Summary
- Abstract
- Description
- Claims
- Application Information
AI Technical Summary
Problems solved by technology
Method used
Image
Examples
specific Embodiment approach 1
[0046] Specific implementation mode one: the following combination Figure 1 to Figure 23 Describe this embodiment, the image processing-based instrument pointer rotation angle recognition method described in this embodiment, the method includes the following steps:
[0047] Step 1. Use an industrial camera to collect a grayscale image of the meter as the original image of the meter; Figure 8 shown.
[0048] Step 2. Preprocessing the original image described in step 1 to obtain a binarized image, such as Figure 9 shown.
[0049] Step 3, initially extracting the scale of the instrument panel on the binarized image, and obtaining an image of the scale of the initially extracted instrument panel; as Figure 10 to Figure 13 shown.
[0050] Step 4. Carry out Hough circle transformation to the initially extracted instrument panel scale image to determine the center of the instrument panel;
[0051] Step 5. According to the center of the instrument panel, the original image de...
specific Embodiment approach 2
[0057] Specific implementation mode 2: This implementation mode further explains the implementation mode 1. The process of preprocessing in step 2 and obtaining a binarized image is as follows: see Figure 10 to Figure 13 .
[0058] Step 21, identify a plurality of rectangular frames as regions of interest on the original image;
[0059] Step 22, thresholding with a 2*2 sliding window to obtain the thresholded original image;
[0060] Step 23, extract the outline of the thresholded original image using the Canny operator, and retain the outline of the scale area;
[0061] Step 24: Perform image corrosion on the thresholded original image using a 3*3 template to obtain a corroded thresholded image,
[0062] The 3*3 template traverses the thresholded original image, and if a pixel contains a pixel in the 3*3 region, the pixel is retained; otherwise, the pixel is removed;
[0063] Step 25. Search for connected domains in the erosion-thresholded image to obtain a binarized imag...
specific Embodiment approach 3
[0065] Specific implementation mode three: this implementation mode further explains implementation mode one or two, and the process of initially determining the center of the instrument panel in step four is:
[0066] Step 41, perform Hough circle transformation on the initially extracted instrument panel scale image, and extract a circle that meets the constraint condition, the constraint condition is: the circle contains at least a continuous 180° arc in the image;
[0067] Step 42, judging whether there is a circle meeting the constraints,
[0068] If the judgment result is yes, execute step 43; if the judgment result is no, then reduce the resolution of the initially extracted instrument panel scale image, and then return to execute step 41;
[0069] Step 43. Based on the Hough transformed circle, search for connected domains in the binarized image to obtain an accurate scale image of the instrument panel, and search for connected domains in the binarized image to obtain ...
PUM
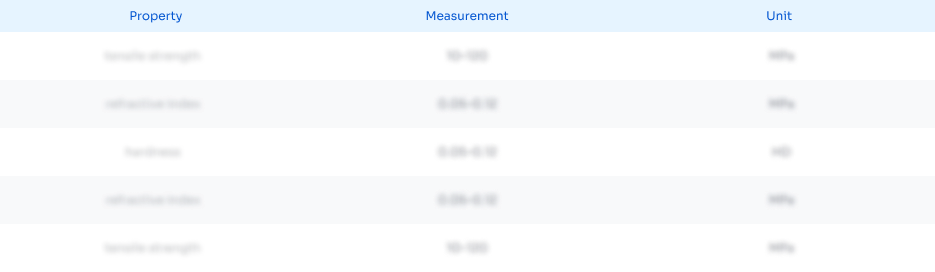
Abstract
Description
Claims
Application Information

- Generate Ideas
- Intellectual Property
- Life Sciences
- Materials
- Tech Scout
- Unparalleled Data Quality
- Higher Quality Content
- 60% Fewer Hallucinations
Browse by: Latest US Patents, China's latest patents, Technical Efficacy Thesaurus, Application Domain, Technology Topic, Popular Technical Reports.
© 2025 PatSnap. All rights reserved.Legal|Privacy policy|Modern Slavery Act Transparency Statement|Sitemap|About US| Contact US: help@patsnap.com