Device and method for power generation by waste heat of blast furnace slag
A waste heat power generation and blast furnace slag technology, which is applied in the field of blast furnace slag waste heat power generation device and high temperature molten iron waste heat recovery, can solve the problem of low heat energy utilization rate and achieve the effect of improving energy utilization rate
- Summary
- Abstract
- Description
- Claims
- Application Information
AI Technical Summary
Problems solved by technology
Method used
Image
Examples
Embodiment 1
[0030] like figure 1 As shown, the blast furnace slag waste heat power generation device includes a first water pump 1, a hot water pool 2, a first heat exchanger 3, a hot water storage tank 4, a second water pump 5, a feed water pump 6, a high-pressure nitrogen source 7, and a second heat exchanger 8. Blast furnace slag 9, thermal deaerator 10, high temperature water storage tank 11, first flash tank 12, second flash tank 13, steam turbine 14, generator 15, condenser 16, condensate pump 17, cooling Tower 18 and so on constitute. The specific process steps and parameters are:
[0031] The first water pump 1 passes through the first heat exchanger 3 through the first heat exchanger 3 and conducts heat exchange with the slag flushing water at about 80°C in the hot water pool 2. The desalinated water is heated to about 70°C and then enters the hot water storage tank 4, and then the desalinated water is heated to about 70°C. The second water pump 5 is sent to the deaerator 10 fo...
PUM
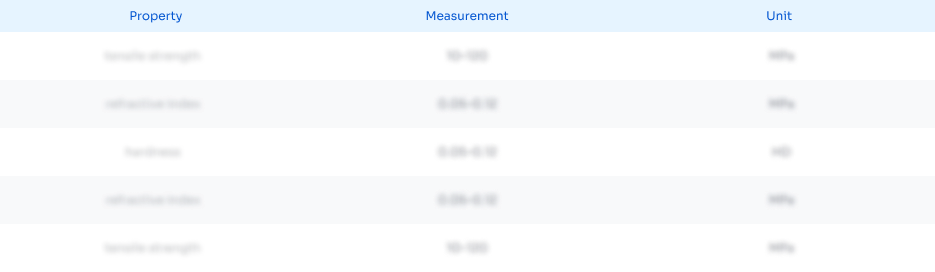
Abstract
Description
Claims
Application Information

- R&D Engineer
- R&D Manager
- IP Professional
- Industry Leading Data Capabilities
- Powerful AI technology
- Patent DNA Extraction
Browse by: Latest US Patents, China's latest patents, Technical Efficacy Thesaurus, Application Domain, Technology Topic, Popular Technical Reports.
© 2024 PatSnap. All rights reserved.Legal|Privacy policy|Modern Slavery Act Transparency Statement|Sitemap|About US| Contact US: help@patsnap.com