Kiln roasting method by glass fiber tank kiln channel
A glass fiber and pool kiln technology, applied in glass furnace equipment, glass manufacturing equipment, manufacturing tools, etc., can solve the problems of low temperature control accuracy, frequent adjustment of passage structure, and high consumption of gas, and achieve less adjustment of passage structure. , The effect of less hidden dangers in the passage and less gas consumption
- Summary
- Abstract
- Description
- Claims
- Application Information
AI Technical Summary
Problems solved by technology
Method used
Image
Examples
Embodiment Construction
[0015] refer to figure 1 , the glass fiber pool kiln path baking kiln method, it is characterized in that: adopt the pool kiln path 1 normal production to carry out baking kiln with combustion gun 3, described method is carried out according to the following steps:
[0016] a. When igniting the kiln, insert the combustion gun 3 at the gun brick 2 of the pool kiln passage 1, and the gas flow rate of a single combustion gun 3 is 0.1~0.5Nm 3 / h, the distance between the combustion guns 3 is 0.1 ~ 1m;
[0017] b. When baking the kiln, first keep the gas flow rate of the single burner 3 unchanged, and increase the number of burner 3 at the gun brick 2 to control the temperature rise;
[0018] c. When the combustion gun 3 at the gun brick 2 of the pool kiln passage 1 is filled up, the temperature rise is controlled by increasing the gas flow rate of a single combustion gun 3 until the kiln is finished.
[0019] Further, the increasing frequency and quantity of the combustion guns ...
PUM
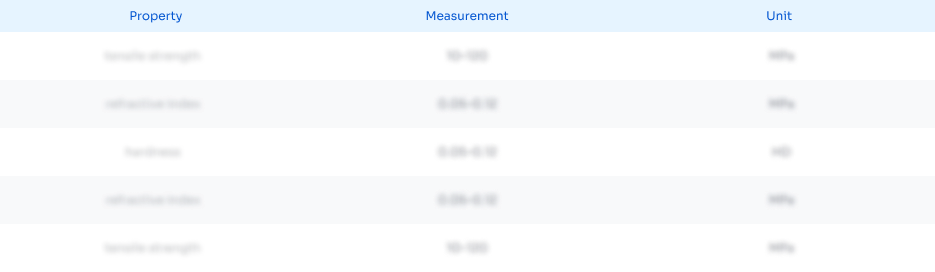
Abstract
Description
Claims
Application Information

- R&D Engineer
- R&D Manager
- IP Professional
- Industry Leading Data Capabilities
- Powerful AI technology
- Patent DNA Extraction
Browse by: Latest US Patents, China's latest patents, Technical Efficacy Thesaurus, Application Domain, Technology Topic, Popular Technical Reports.
© 2024 PatSnap. All rights reserved.Legal|Privacy policy|Modern Slavery Act Transparency Statement|Sitemap|About US| Contact US: help@patsnap.com