Hook height limit detection device and dynamic compactor
A detection device and detection mechanism technology, applied in the field of construction machinery, can solve the problems of wrong command of the control system, wrong signal sent by the height limit switch, unable to work normally, etc., to achieve effective detection and control, reduce error signals, and eliminate error signals Effect
- Summary
- Abstract
- Description
- Claims
- Application Information
AI Technical Summary
Problems solved by technology
Method used
Image
Examples
Embodiment Construction
[0023] The technical solutions of the present invention will be described in further detail below with reference to the accompanying drawings and embodiments.
[0024] like figure 1 As shown, it is a structural schematic view of an embodiment of the hook height limit detection device of the present invention in an installed state. In this embodiment, the hook height limit detection device includes a rope pressing mechanism 4 and a position detection mechanism 5, wherein the rope pressing mechanism 4 includes a pressing part for pressing the hoisting wire rope wound on the hoisting winch 1 and The part to be detected, wherein the part to be detected is connected with the pressing part, and changes as the position of the pressing part in the radial direction of the hoisting hoist 1 changes. The position detection mechanism 5 includes a detection switch for detecting whether the portion to be detected approaches.
[0025] figure 1 The middle lifting winch 1 can be fixed on the...
PUM
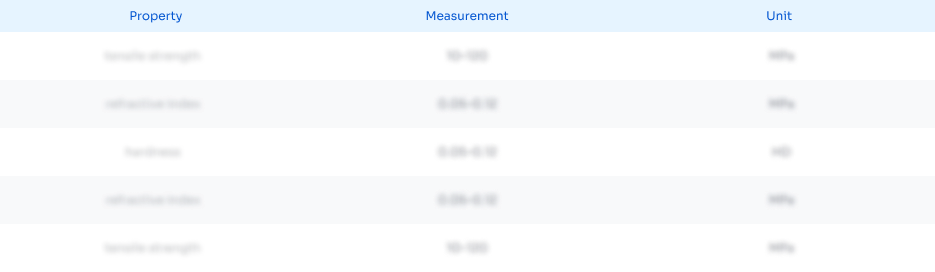
Abstract
Description
Claims
Application Information

- R&D Engineer
- R&D Manager
- IP Professional
- Industry Leading Data Capabilities
- Powerful AI technology
- Patent DNA Extraction
Browse by: Latest US Patents, China's latest patents, Technical Efficacy Thesaurus, Application Domain, Technology Topic, Popular Technical Reports.
© 2024 PatSnap. All rights reserved.Legal|Privacy policy|Modern Slavery Act Transparency Statement|Sitemap|About US| Contact US: help@patsnap.com