Liquid enzyme stabilizing additive and preparation method and application thereof
A liquid enzyme and additive technology, applied in chemical instruments and methods, applications, cosmetic preparations, etc., can solve the problems affecting the production and development of liquid detergent formulations with liquid enzymes, poor stability, loss of vitality, etc.
- Summary
- Abstract
- Description
- Claims
- Application Information
AI Technical Summary
Problems solved by technology
Method used
Image
Examples
Embodiment 1
[0020] Ether nonionic surfactant EO 76 PO 30 EO 76 Dissolve 1g in 10g of deionized water, then take 1g of liquid protease (ATCC2152 alkaline protease fermentation broth) and mix it, add the mixture dropwise to 0.6g of α-cyclodextrin, then add 15g of sodium dodecylbenzene sulfate surfactant (HLB value 10.6) Mix well.
[0021] The above liquid enzyme stabilizing additives were transferred to two vials, sealed and incubated at 5°C and 27°C for 4 weeks respectively. The enzyme activity of protease samples was determined by the national standard GB / T23527-2009 (see Table 1).
[0022] Control: Dissolve 1 g of liquid protease (enzyme liquid produced by alkaline protease fermentation broth ATCC2152) in 10 g of deionized water, then add 15 g of sodium dodecylbenzene sulfate surfactant (HLB value 10.6) and mix evenly. The determination method is the same as above.
[0023] Table 1
[0024]
Embodiment 2
[0026] Ether nonionic surfactant PEO 133 PPOs 50 PEOs 133 Dissolve 0.6g in 15g of deionized water, take 1.2g of liquid α-amylase (Bacillus subtilis) and mix it, add the mixture dropwise to 1.8g of hydroxypropyl-cyclodextrin, and then add 10g of C12 fatty alcohol polyoxyethylene ether 9 (HLB value 13.5) and 10g C12 alkyl glycoside surfactant (HLB value 16) were mixed.
[0027] The above liquid enzyme stabilizing additives were transferred to two vials, sealed and incubated at 5°C and 27°C for 4 weeks respectively. The enzyme activity of amylase samples was determined by the national standard GB8275-2009 method (see Table 2).
[0028] Control: Dissolve 1.2g of liquid amylase protease in 15g of deionized water, then add 10g of C12 fatty alcohol polyoxyethylene ether 9 (HLB value 13.5) and 10g of C12 alkyl glycoside surfactant (HLB value 16) and mix evenly Ditto.
[0029] Table 2
[0030]
Embodiment 3
[0032] Ether nonionic surfactant PEO 27 PPOs 61 PEOs 27 Dissolve 2 g in 10 g of deionized water, mix 1 g of liquid cellulase (1,4-β-D-glucan glucoside hydrolase) with it, add the mixture dropwise to 0.6 g of 15-crown ether-5, and then add 12g C12 fatty alcohol polyoxyethylene ether 3 (HLB value 8.5) and 10g sodium dodecylsulfonate (HLB value 13) surfactant were mixed evenly.
[0033] The above liquid enzyme stabilizing additives were transferred to two vials, sealed and incubated at 5°C and 27°C for 4 weeks respectively. After storage, the enzyme activity of the cellulase samples was determined by QB2583-2003 (the industry standard of the Ministry of Light Industry) (see Table 3).
[0034] Control: Dissolve 1g of liquid amylase protease in 10g of deionized water, then add 12g of C12 fatty alcohol polyoxyethylene ether 3 and 10g of sodium dodecylsulfonate (HLB value 13) surfactant and mix well, and the determination method is the same as above.
[0035] table 3
[0036] ...
PUM
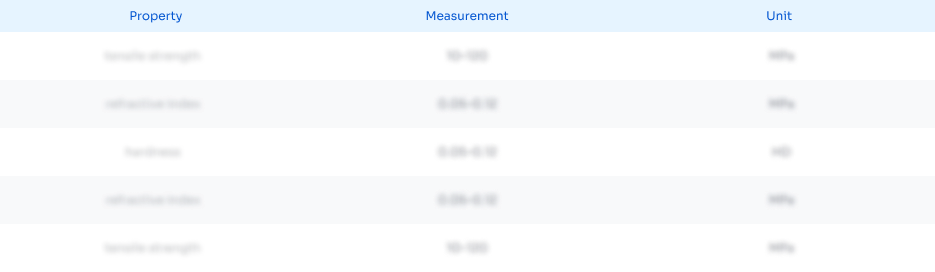
Abstract
Description
Claims
Application Information

- R&D
- Intellectual Property
- Life Sciences
- Materials
- Tech Scout
- Unparalleled Data Quality
- Higher Quality Content
- 60% Fewer Hallucinations
Browse by: Latest US Patents, China's latest patents, Technical Efficacy Thesaurus, Application Domain, Technology Topic, Popular Technical Reports.
© 2025 PatSnap. All rights reserved.Legal|Privacy policy|Modern Slavery Act Transparency Statement|Sitemap|About US| Contact US: help@patsnap.com