Centrifugal pendulum mechanism
A centrifugal force pendulum and pendulum mass technology, applied in springs/shock absorbers, vibration suppression adjustment, mechanical equipment, etc., can solve problems such as damage to the connecting pendulum support, tipping of the pendulum mass pendulum mass bracket, damage to the centrifugal force pendulum function and mode, etc.
- Summary
- Abstract
- Description
- Claims
- Application Information
AI Technical Summary
Problems solved by technology
Method used
Image
Examples
Embodiment Construction
[0058] figure 1 A partial front view of a rotational speed-adapted shock absorber provided according to the invention in the form of a centrifugal pendulum device 1 is shown in schematic diagram. This preferably comprises a plurality of inertial masses acting as pendulum masses 2 , which are mounted movably relative to a rotatable pendulum mass support 3 on the pendulum mass support 3 . The support is implemented pivotally. The pendulum mass support 3 is preferably designed as an annular disk-shaped element. The individual pendulum masses 2 are arranged on the pendulum mass carrier in a uniformly spaced manner as seen in the circumferential direction about the axis of rotation R. FIG. Only pendulum mass 2A of one pendulum mass unit 2 is depicted in the partial diagram of the present presentation. The depiction of the axis of rotation R is only intended to achieve a schematic representation and is not to a correct standard dimension. The inventive support arrangement of the...
PUM
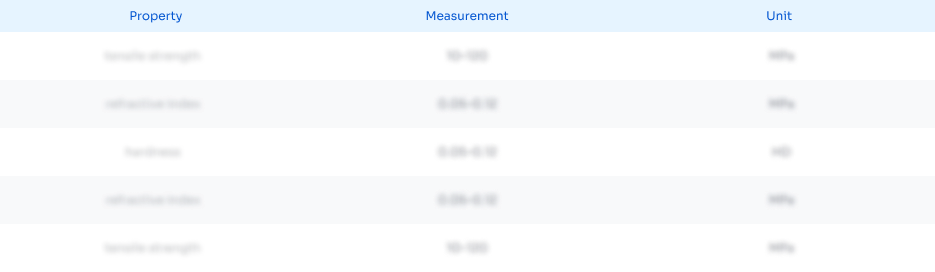
Abstract
Description
Claims
Application Information

- Generate Ideas
- Intellectual Property
- Life Sciences
- Materials
- Tech Scout
- Unparalleled Data Quality
- Higher Quality Content
- 60% Fewer Hallucinations
Browse by: Latest US Patents, China's latest patents, Technical Efficacy Thesaurus, Application Domain, Technology Topic, Popular Technical Reports.
© 2025 PatSnap. All rights reserved.Legal|Privacy policy|Modern Slavery Act Transparency Statement|Sitemap|About US| Contact US: help@patsnap.com