Bearing propelled stirring quenching device
A push-type stirring and quenching device technology, which is applied in the direction of quenching devices, heat treatment equipment, furnaces, etc., can solve the problems of slow and slow series cooling frequency, and the finished product cannot meet the design requirements, and achieve the effect of small convective loss
- Summary
- Abstract
- Description
- Claims
- Application Information
AI Technical Summary
Problems solved by technology
Method used
Image
Examples
Embodiment Construction
[0024] A bearing-propelled stirring quenching device, comprising a quenching oil pool 1, a first oil propeller 2, a second oil propeller 3, a third oil propeller 4, a first deflector 5, a second deflector 6, The third deflector 7 and the shield 8 of the upper opening are characterized in that:
[0025] The pool wall 9 of the quenching oil pool 1 is cylindrical, and three oil outlet holes are arranged equidistantly along the circumferential direction on the upper part of the pool wall 9; the first elbow through holes are opened equidistantly along the circumferential direction on the lower part of the pool wall 9 10. The second elbow through hole 11 and the third elbow through hole 12, the angle between the centers of the first elbow through hole 10, the second elbow through hole 11 and the third elbow through hole 12 is 120° °;
[0026] The first oil thruster comprises oil delivery tube 13, propeller rotating shaft 14, propeller blade 15, upper bearing seat 16, lower bearing ...
PUM
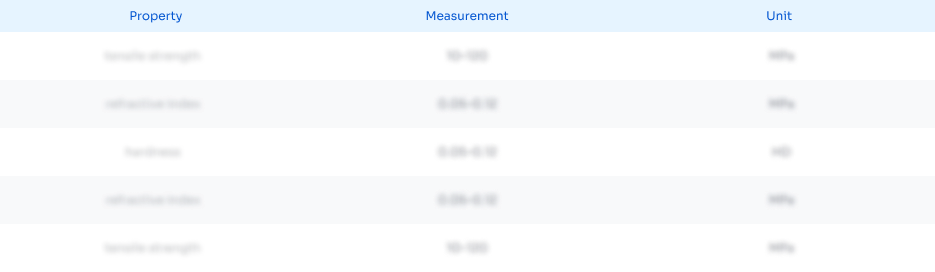
Abstract
Description
Claims
Application Information

- R&D
- Intellectual Property
- Life Sciences
- Materials
- Tech Scout
- Unparalleled Data Quality
- Higher Quality Content
- 60% Fewer Hallucinations
Browse by: Latest US Patents, China's latest patents, Technical Efficacy Thesaurus, Application Domain, Technology Topic, Popular Technical Reports.
© 2025 PatSnap. All rights reserved.Legal|Privacy policy|Modern Slavery Act Transparency Statement|Sitemap|About US| Contact US: help@patsnap.com