Injection molding machine
A technology of injection molding machine and servo motor, applied in the field of injection molding machine, can solve the problems of low repeatability, easily damaged hydraulic components, damaged asynchronous motor, etc., and achieve the effect of prolonging the life of hydraulic system, good energy saving performance and high repeatability
- Summary
- Abstract
- Description
- Claims
- Application Information
AI Technical Summary
Problems solved by technology
Method used
Image
Examples
Embodiment 1
[0016] Such as figure 1 As shown, the injection molding machine described in this embodiment includes a servo control system, and the servo control system includes a control valve 1, an oil tank 2, an oil outlet pipe 3, an oil return pipe 4, a quantitative pump 5 and a hydraulic pressure as the power of the injection molding machine. The oil cylinder 6, the oil outlet pipe 3 and the oil return pipe 4 are connected between the control valve 1 and the oil tank 2, and the hydraulic oil cylinder 6 is provided with two front and rear chambers separated by the piston, and the two chambers are respectively connected to the control valve. The valve 1 is connected, the quantitative pump 5 is arranged on the oil outlet pipe 3, the servo control system also includes a servo motor 7, a rotary encoder 8, a servo drive controller 9 and a pressure sensor 10, and the servo motor 7 is connected to the quantitative The pump 5 is connected by transmission; the rotary encoder 8 is set on the serv...
PUM
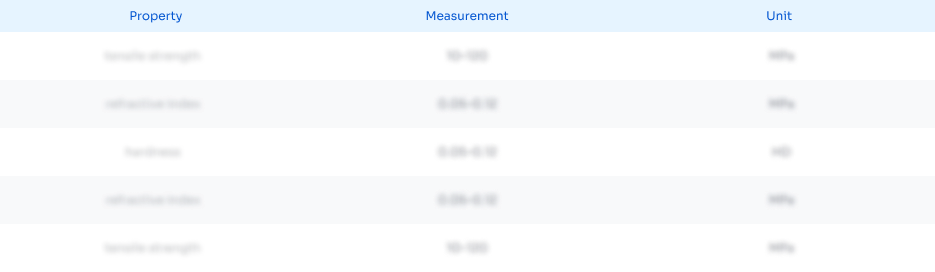
Abstract
Description
Claims
Application Information

- R&D
- Intellectual Property
- Life Sciences
- Materials
- Tech Scout
- Unparalleled Data Quality
- Higher Quality Content
- 60% Fewer Hallucinations
Browse by: Latest US Patents, China's latest patents, Technical Efficacy Thesaurus, Application Domain, Technology Topic, Popular Technical Reports.
© 2025 PatSnap. All rights reserved.Legal|Privacy policy|Modern Slavery Act Transparency Statement|Sitemap|About US| Contact US: help@patsnap.com