A front longitudinal beam outer panel structure
A front longitudinal beam and plate structure technology, which is applied in the substructure, transportation and packaging, vehicle components, etc., can solve the problems of non-direct transmission path and low transmission efficiency, so as to optimize the transmission path, improve the collision performance, and improve the energy transmission. The effect of efficiency
- Summary
- Abstract
- Description
- Claims
- Application Information
AI Technical Summary
Problems solved by technology
Method used
Image
Examples
Embodiment Construction
[0021] see Figure 4 and Figure 5 , which shows a preferred embodiment of a front longitudinal beam outer panel structure of the present invention, including a front longitudinal beam body, which includes a front longitudinal beam outer panel 1 and a front longitudinal beam inner panel 2, such as image 3 As shown, similar to the prior art, the front side member outer panel 1 and the front side member inner panel 2 of the present invention are also arranged in an approximately parallel manner in the front and rear direction of the vehicle, and extend rearward. It should be pointed out that in the present invention, Figure 4 and Figure 5 The left side of is the front direction of the vehicle; Figure 4 The upper side of is the direction outside the vehicle. Further, the rear section 4 of the front longitudinal beam outer panel 1 is fixedly connected to the door sill panel 6 and / or the front door hinge column 7 of the motor vehicle. In this embodiment, preferably, the fro...
PUM
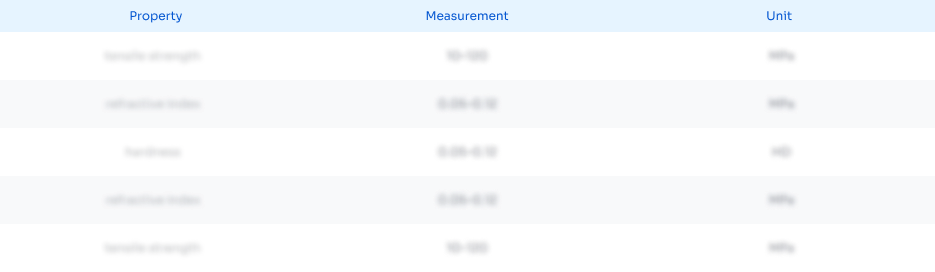
Abstract
Description
Claims
Application Information

- R&D
- Intellectual Property
- Life Sciences
- Materials
- Tech Scout
- Unparalleled Data Quality
- Higher Quality Content
- 60% Fewer Hallucinations
Browse by: Latest US Patents, China's latest patents, Technical Efficacy Thesaurus, Application Domain, Technology Topic, Popular Technical Reports.
© 2025 PatSnap. All rights reserved.Legal|Privacy policy|Modern Slavery Act Transparency Statement|Sitemap|About US| Contact US: help@patsnap.com