On-site self-calibration method for measurement system error of precise rotary table
A technology of rotating table and measuring system, applied in the direction of measuring devices, instruments, etc., can solve the problem of lack of self-calibration method of rotating table, and achieve the effect of high-precision system error self-calibration and high-precision calibration work
- Summary
- Abstract
- Description
- Claims
- Application Information
AI Technical Summary
Problems solved by technology
Method used
Image
Examples
Embodiment Construction
[0024] The technical solutions of the present invention will be described in further detail below according to the accompanying drawings and in conjunction with specific implementation steps.
[0025] A method for in-situ self-calibration of errors of a precision rotary table measurement system disclosed by the invention is realized by the following technical solutions:
[0026] A method for in-situ self-calibration of errors in a precision rotary table measurement system, characterized in that the self-calibration method comprises the following steps:
[0027] 1) Prepare a glass plate 1, which has N equally divided fan-shaped score lines 2, and the angle between each score line is 360 / N°, where N is a positive integer constant, and the glass plate fan-shaped score line The deviation from the ideal graticule is recorded as auxiliary error A n , where n=0,1,…,N-1;
[0028] 2) The glass plate 1 is fixedly placed on the calibrated rotary table 5, and an angle sensor 4 is instal...
PUM
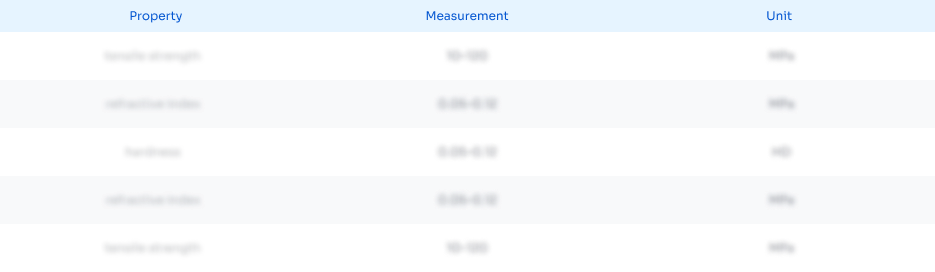
Abstract
Description
Claims
Application Information

- Generate Ideas
- Intellectual Property
- Life Sciences
- Materials
- Tech Scout
- Unparalleled Data Quality
- Higher Quality Content
- 60% Fewer Hallucinations
Browse by: Latest US Patents, China's latest patents, Technical Efficacy Thesaurus, Application Domain, Technology Topic, Popular Technical Reports.
© 2025 PatSnap. All rights reserved.Legal|Privacy policy|Modern Slavery Act Transparency Statement|Sitemap|About US| Contact US: help@patsnap.com