Automatic accurate adjustment system for instrument movement clearance
A technology of automatic adjustment and movement, applied in the mechanical field, can solve the problem of large precision adjustment error, and achieve the effect of short processing cycle, low cost and high production efficiency
- Summary
- Abstract
- Description
- Claims
- Application Information
AI Technical Summary
Problems solved by technology
Method used
Image
Examples
Embodiment 1
[0019] Such as figure 1 and figure 2 As shown, a precision automatic adjustment system for instrument movement gaps of the present invention is composed of a head module 200, a base module 300, a paddle module 400, a laser displacement sensor module 500 and a controller 600, as image 3 As shown, the base module 300 is composed of a turntable 5, a flange 2, a zero sensor 3, a part positioning fixture 4, a positioning cylinder 6 and a first stepping motor 1, the flange 2 is arranged on the workbench 100, and the turntable 5. The zero sensor 3, the positioning cylinder 6 and the first stepping motor 1 are arranged on the flange 2, and the lower side of the turntable 5 is provided with a zero groove, and the distance between the zero groove and the center of the turntable is equal to the zero sensor 3 The distance from the center of the turntable 5 in the horizontal direction, the part positioning fixture 4 is arranged on the upper side of the turntable 5, the turntable 5 is co...
PUM
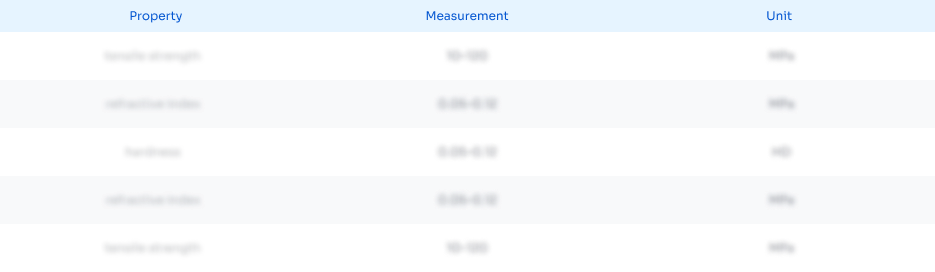
Abstract
Description
Claims
Application Information

- Generate Ideas
- Intellectual Property
- Life Sciences
- Materials
- Tech Scout
- Unparalleled Data Quality
- Higher Quality Content
- 60% Fewer Hallucinations
Browse by: Latest US Patents, China's latest patents, Technical Efficacy Thesaurus, Application Domain, Technology Topic, Popular Technical Reports.
© 2025 PatSnap. All rights reserved.Legal|Privacy policy|Modern Slavery Act Transparency Statement|Sitemap|About US| Contact US: help@patsnap.com