Form erecting method for casting dome roof in situ
A formwork support method and cast-in-place technology, which is applied in the field preparation of formwork/formwork/working frame, building components, construction, etc., can solve the problems of high labor intensity, difficult construction, and slow construction progress. Achieve the effect of ensuring the safety of structure construction, ensuring the quality of structure forming, and speeding up the construction progress
- Summary
- Abstract
- Description
- Claims
- Application Information
AI Technical Summary
Problems solved by technology
Method used
Examples
Embodiment Construction
[0016] The present invention is described in further detail below in conjunction with specific embodiments;
[0017] 1. The principle of mold matching and the retention of construction joints
[0018] Both the inner and outer formwork are prefabricated on site and assembled in sections by means of enlarged samples. In order to facilitate construction, the inner formwork is assembled and installed to the top at one time, and the outer formwork and concrete are constructed in sections, and the formwork is used for turnover. The height of the segment is determined as the arc length of the dome is 4480mm according to the specifications of the plywood. The plywood should be used directly in the whole piece, and random sawing should be minimized. The lower half of the hemispherical dome adopts a double-sided formwork, and when the chord inclination angle corresponding to the upper arc is less than 30°, a single-sided formwork is used.
[0019] 2. Make the back corrugation of the sl...
PUM
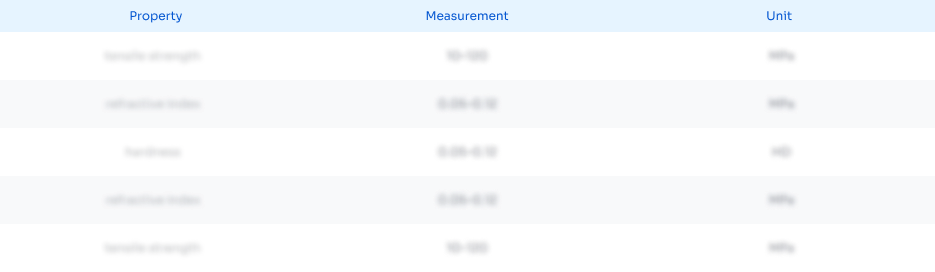
Abstract
Description
Claims
Application Information

- Generate Ideas
- Intellectual Property
- Life Sciences
- Materials
- Tech Scout
- Unparalleled Data Quality
- Higher Quality Content
- 60% Fewer Hallucinations
Browse by: Latest US Patents, China's latest patents, Technical Efficacy Thesaurus, Application Domain, Technology Topic, Popular Technical Reports.
© 2025 PatSnap. All rights reserved.Legal|Privacy policy|Modern Slavery Act Transparency Statement|Sitemap|About US| Contact US: help@patsnap.com