Waste cathode-ray tube cone glass machinery activation wet-process sulphur treatment method
A mechanical activation and vulcanization technology, applied in the direction of improving process efficiency, can solve problems such as high energy consumption and complex equipment, and achieve the effect of high activation efficiency, wide application and mature process technology.
- Summary
- Abstract
- Description
- Claims
- Application Information
AI Technical Summary
Problems solved by technology
Method used
Image
Examples
Example Embodiment
[0020] Example 1
[0021] Take 4g of the crushed waste cathode ray tube cone glass and add it to the planetary high-energy ball mill ball milling tank. The filling ratio of the ball milling medium (zirconia) and the CRT cone glass particles is 20:1, the mechanical ball milling speed is 500rpm, and the mechanical activation time is 2 hours. Obtain mechanically activated CRT cone glass powder.
[0022] The water, CRT cone glass powder and elemental sulfur powder were added to the autoclave at a mass ratio of 100:30:1, the pressure of the reactor was 12MPa, and the solid-liquid reaction was carried out under mechanical stirring at 300°C for 2 hours. After the above-mentioned leaching reaction is completed, filtration is performed to realize solid-liquid separation of the mixed liquid.
[0023] After analysis, the sulfidation rate of metallic lead in CRT cone glass is 26.2%.
Example Embodiment
[0024] Example 2
[0025] Take 4g of the crushed waste cathode ray tube cone glass and add it to the planetary high-energy ball mill ball milling tank. The filling ratio of the ball milling medium (zirconia) and the CRT cone glass particles is 20:1, the mechanical ball milling speed is 500rpm, and the mechanical activation time is 2 hours. Obtain mechanically activated CRT cone glass powder.
[0026] The water, CRT cone glass powder and elemental sulfur powder were added to the autoclave at a mass ratio of 300:10:1, the pressure of the reactor was 6MPa, and the solid-liquid reaction was carried out at 220°C for 2 hours under mechanical stirring conditions. After the above-mentioned leaching reaction is completed, filtration is performed to realize solid-liquid separation of the mixed liquid.
[0027] After analysis, the sulfidation rate of metallic lead in CRT cone glass is 64.9%.
Example Embodiment
[0028] Example 3
[0029] Take 4g of the crushed waste cathode ray tube cone glass and add it to the planetary high-energy ball mill ball milling tank. The filling ratio of the ball milling medium (zirconia) and the CRT cone glass particles is 20:1, the mechanical ball milling speed is 500rpm, and the mechanical activation time is 2 hours. Obtain mechanically activated CRT cone glass powder.
[0030] Water, CRT cone glass powder and elemental sulfur powder were added to the autoclave at a mass ratio of 100:30:1, the pressure of the reactor was 1MPa, and the solid-liquid reaction was carried out at 300°C for 2 hours under mechanical stirring conditions. After the above-mentioned leaching reaction is completed, filtration is performed to realize solid-liquid separation of the mixed liquid.
[0031] After analysis, the sulfurization rate of metallic lead in CRT cone glass is 88.9%.
PUM
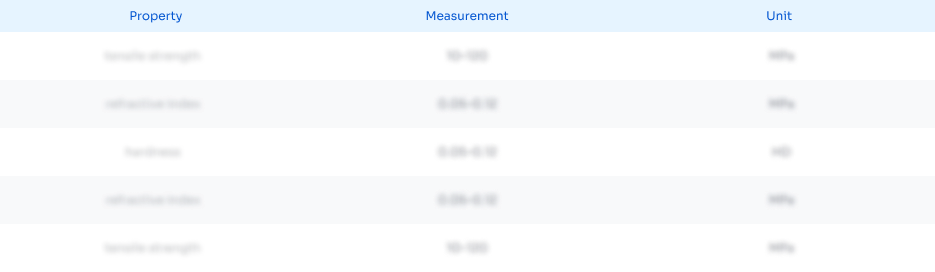
Abstract
Description
Claims
Application Information

- R&D
- Intellectual Property
- Life Sciences
- Materials
- Tech Scout
- Unparalleled Data Quality
- Higher Quality Content
- 60% Fewer Hallucinations
Browse by: Latest US Patents, China's latest patents, Technical Efficacy Thesaurus, Application Domain, Technology Topic, Popular Technical Reports.
© 2025 PatSnap. All rights reserved.Legal|Privacy policy|Modern Slavery Act Transparency Statement|Sitemap|About US| Contact US: help@patsnap.com