Condensation cavity for gas water heater and manufacturing technology thereof
A gas water heater and processing technology, applied in fluid heaters, applications, household appliances, etc., can solve the problems of difficult operation, time-consuming and laborious, and low production efficiency for workers, so as to improve product competitiveness, easy for workers to operate, and reduce production costs. The effect of product cost
- Summary
- Abstract
- Description
- Claims
- Application Information
AI Technical Summary
Problems solved by technology
Method used
Image
Examples
Embodiment Construction
[0014] Such as figure 1 As shown, the condensing chamber for a gas water heater of the present invention includes an upper cover 1, a barrel body 2 and a lower cover 3, the upper cover 1 is provided with a first flange 11, and the barrel body 2 is provided with a second flange 21 and a third flange. Flange 22, the lower cover 3 is provided with a fourth flange 31, the first flange 11 of the upper cover 1 and the second flange 21 of the barrel body 2 are tightly crimped together by a rolling machine; the fourth flange of the lower cover 3 The folded edge 31 and the third folded edge 22 of the barrel body 2 are tightly crimped together by a rolling machine. Both the first folded edge 11 of the upper cover 1 and the fourth folded edge 31 of the lower cover 3 are bent inward; the second folded edge 21 and the third folded edge 22 of the barrel body 2 are bent outward.
[0015] A process for processing a condensing cavity for a gas water heater, comprising the following process st...
PUM
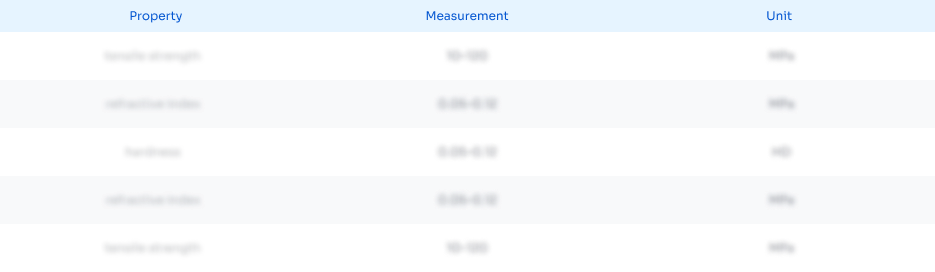
Abstract
Description
Claims
Application Information

- R&D
- Intellectual Property
- Life Sciences
- Materials
- Tech Scout
- Unparalleled Data Quality
- Higher Quality Content
- 60% Fewer Hallucinations
Browse by: Latest US Patents, China's latest patents, Technical Efficacy Thesaurus, Application Domain, Technology Topic, Popular Technical Reports.
© 2025 PatSnap. All rights reserved.Legal|Privacy policy|Modern Slavery Act Transparency Statement|Sitemap|About US| Contact US: help@patsnap.com