Process utilizing chemical gypsum to produce high strength alpha gypsum
A chemical gypsum and process technology, applied in the direction of manufacturing tools, ceramic molding machines, etc., can solve the problems of unstable product quality, low production line capacity, low heat source efficiency, etc., to improve resource utilization, high production efficiency, and resource utilization. high effect
- Summary
- Abstract
- Description
- Claims
- Application Information
AI Technical Summary
Problems solved by technology
Method used
Examples
specific Embodiment approach 2
[0040] a. Fully mix chemical gypsum, water, and additives so that the solid content of the mixed product is 70% and the temperature is 90 degrees Celsius to form a stable slurry to be reacted, and the additives account for 0.1% of the gypsum mass;
[0041] b. Mix the slurry to be reacted in step a with additives, and perform crystal transformation after mixing. Conditions for crystal transformation: pressure: 0.5Mpa, temperature 110 degrees Celsius, and crystal transformation time for 5 hours. The additive accounts for 0.01% of the gypsum mass; The heating tube is wound outside the crystal tank, and the bottom of the tank is equipped with a steam nozzle; the crystal conversion process is a metered continuous crystal conversion: the slurry to be reacted and additives are continuously added to the crystal conversion tank according to the ratio of the two
[0042] c. After the step b is crystallized, the slurry is sent to the molding machine after being centrifuged with hot ...
specific Embodiment approach 3
[0047] a. Fully mix chemical gypsum, water, and additives so that the solid content of the mixed product is 50% and the temperature is 80 degrees Celsius to form a stable slurry to be reacted, and the additives account for 0.05% of the gypsum mass;
[0048] b. Mix the slurry to be reacted in step a with additives, and perform crystal transformation after mixing. Conditions for crystal transformation: pressure: 0.3Mpa, temperature 130 degrees Celsius, and crystal transformation time for 2 hours. The additive accounts for 0.06% of the gypsum mass; The heating tube is wound outside the crystal tank, and the bottom of the tank is equipped with a steam nozzle; the crystal conversion process is a metered continuous crystal conversion: the slurry to be reacted and additives are continuously added to the crystal conversion tank according to the ratio of the two
[0049] c. The slurry after the crystallization in step b is sent to a molding machine after being sent to a centrifuge...
specific Embodiment approach 4
[0054] a. Fully mix chemical gypsum, water, and additives so that the solid content of the mixed product is 40% and the temperature is 85 degrees Celsius to form a stable slurry to be reacted, and the additives account for 0.03% of the gypsum mass;
[0055] b. Mix the slurry to be reacted in step a with additives, and perform crystal transformation after mixing. Conditions for crystal transformation: pressure: 0.4Mpa, temperature 120 degrees Celsius, and crystal transformation time for 3 hours. The additive accounts for 0.08% of the gypsum mass; The heating tube is wound outside the crystal tank, and the bottom of the tank is equipped with a steam nozzle; the crystal conversion process is a metered continuous crystal conversion: the slurry to be reacted and additives are continuously added to the crystal conversion tank according to the ratio of the two
[0056] c. The slurry after step b is crystallized is sent to a molding machine after being sent to a 400°C hot air cen...
PUM
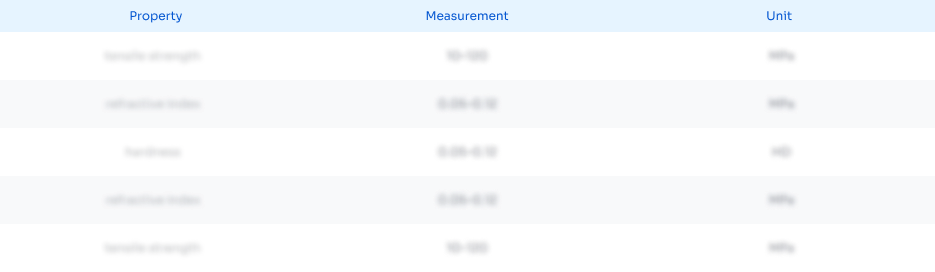
Abstract
Description
Claims
Application Information

- R&D
- Intellectual Property
- Life Sciences
- Materials
- Tech Scout
- Unparalleled Data Quality
- Higher Quality Content
- 60% Fewer Hallucinations
Browse by: Latest US Patents, China's latest patents, Technical Efficacy Thesaurus, Application Domain, Technology Topic, Popular Technical Reports.
© 2025 PatSnap. All rights reserved.Legal|Privacy policy|Modern Slavery Act Transparency Statement|Sitemap|About US| Contact US: help@patsnap.com