Non-hydrodenitrogeneration method for catalytically cracked gasoline
A catalytically cracked gasoline, non-hydrogenation technology is applied in the non-hydrogenation denitrification field of catalytically cracked gasoline, which can solve problems such as difficulty in operation, and achieve the effects of improving economic efficiency, prolonging service life and reducing material loss.
- Summary
- Abstract
- Description
- Claims
- Application Information
AI Technical Summary
Problems solved by technology
Method used
Examples
Embodiment 1
[0025] Preparation of liquid denitrification agent: Weigh 100 g of 85% phosphoric acid, add 5 g of water, stir and mix, and dissolve 5 g of copper pyrophosphate in the above phosphoric acid solution. Wherein the mass percentage of orthophosphoric acid is 77.3%, the mass percentage of copper pyrophosphate is 4.5%, and the mass percentage of water is 18.2%.
[0026] Preparation of solid denitrification agent: Weigh 25 g of liquid denitrification agent and add 75 g of water to prepare a 25% aqueous solution, add 50 g of coal-based activated carbon (Ф1.5′3-10), mix in the above aqueous solution, and soak at at 20°C, impregnated for 14 h, filtered and dried at 105°C to constant weight.
[0027] Liquid denitrification agent pre-denitrification: Take 1 L catalytic cracking gasoline, its weight is 711.7g, put it in a 2 L stainless steel reactor, add 0.107 g liquid denitrification agent, the amount of liquid denitrification agent added accounts for the weight percentage of catalytic cr...
Embodiment 2
[0033] Preparation of liquid denitrification agent: Weigh 90 g of 85% phosphoric acid, add 10 g of water, stir and mix, and dissolve 7 g of copper pyrophosphate in the above phosphoric acid solution. Wherein the mass percentage of orthophosphoric acid is 71.5%, the mass percentage of copper pyrophosphate is 6.5%, and the mass percentage of water is 22%.
[0034]Preparation of solid denitrification agent: Weigh 30 g of liquid denitrification agent and add 70 g of water to prepare a 30% aqueous solution, add 66 g of 13X molecular sieve, mix in the above aqueous solution, immerse at 25°C for 24 h, and filter at 105 °C to constant weight.
[0035] Liquid denitrification agent pre-denitrification: Take 1 L catalytic cracking gasoline, its weight is 711.7g, put it in a 2 L stainless steel reactor, add 0.07 g liquid denitrification agent, the amount of liquid denitrification agent added accounts for the weight percentage of catalytic cracking gasoline Stir for 10 minutes at 0.2MPa a...
Embodiment 3
[0039] Preparation of liquid denitrification agent: Weigh 110 g of 85% phosphoric acid, add 5 g of water, stir and mix, and dissolve 10 g of copper pyrophosphate in the above phosphoric acid solution. Wherein the mass percentage of orthophosphoric acid is 74.8%, the mass percentage of copper pyrophosphate is 8.0%, and the mass percentage of water is 17.2%.
[0040] Preparation of solid denitrification agent: Weigh 20 g of liquid denitrification agent and add 80 g of water to prepare a 20% aqueous solution, add 33 g of activated alumina, mix in the above aqueous solution, immerse at 15°C for 20 h, and filter Dry at 105°C to constant weight.
[0041] Liquid denitrification agent pre-denitrification: take 1 L catalytic cracking gasoline, its weight is 711.7g, put it in a 2 L stainless steel reactor, add 0.14 g liquid denitrification agent, the amount of liquid denitrification agent added accounts for the weight percentage of catalytic cracking gasoline 0.02%, stirred at 0.3MPa a...
PUM
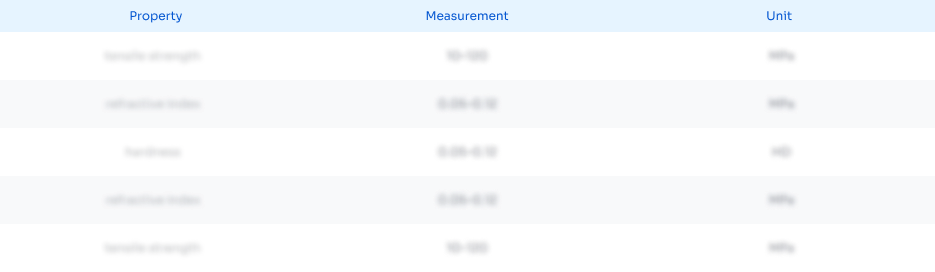
Abstract
Description
Claims
Application Information

- R&D
- Intellectual Property
- Life Sciences
- Materials
- Tech Scout
- Unparalleled Data Quality
- Higher Quality Content
- 60% Fewer Hallucinations
Browse by: Latest US Patents, China's latest patents, Technical Efficacy Thesaurus, Application Domain, Technology Topic, Popular Technical Reports.
© 2025 PatSnap. All rights reserved.Legal|Privacy policy|Modern Slavery Act Transparency Statement|Sitemap|About US| Contact US: help@patsnap.com