Automatic conveying mechanical arm suitable for glass mould welding
A technology of glass molds and manipulators, applied in manipulators, program-controlled manipulators, welding equipment, etc., can solve problems such as inability to accurately locate and control, prone to accidents, high mold temperature, etc., and achieve simple structure, improved safety, and reliable control Effect
- Summary
- Abstract
- Description
- Claims
- Application Information
AI Technical Summary
Problems solved by technology
Method used
Image
Examples
Embodiment Construction
[0018] The present invention will be further described below in conjunction with the accompanying drawings and embodiments.
[0019] Such as figure 1 As shown, the present invention includes a base 1, a guide rail 2, a first manipulator 3, a second manipulator 4, a timing belt 5, a turning frame 6, a turning cylinder 7, an L plate 8, a timing belt adjusting device 9, and a timing belt fixing device 10 and welding bed 11.
[0020] The base 1 is a Π-shaped structure, on which a guide rail 2 is installed, and a timing belt 5 is installed on the inside of the guide rail 2, and the first manipulator 3 and the second manipulator 4 are installed on the guide rail 2 by the timing belt 5. Welding bed 11 is arranged at the rear of base 1 middle part, and turning frame 6 is fixed on the rear of base 1 left column foot, and welding bed 11, turning frame 6 and base 1 are placed on the same level. The L plate 8 is hinged to the left end at the top of the turning frame 6 . Overturning cyl...
PUM
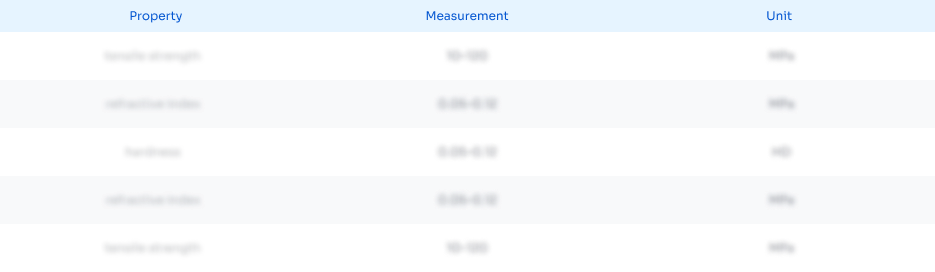
Abstract
Description
Claims
Application Information

- Generate Ideas
- Intellectual Property
- Life Sciences
- Materials
- Tech Scout
- Unparalleled Data Quality
- Higher Quality Content
- 60% Fewer Hallucinations
Browse by: Latest US Patents, China's latest patents, Technical Efficacy Thesaurus, Application Domain, Technology Topic, Popular Technical Reports.
© 2025 PatSnap. All rights reserved.Legal|Privacy policy|Modern Slavery Act Transparency Statement|Sitemap|About US| Contact US: help@patsnap.com