Method for adjusting poses of airplane components based on 3-2-1 following locator
A technology for adjusting aircraft parts and poses, applied to aircraft parts, aircraft assembly, ground installations, etc., can solve problems such as waste, increased production costs, and systems that cannot be reused
- Summary
- Abstract
- Description
- Claims
- Application Information
AI Technical Summary
Problems solved by technology
Method used
Image
Examples
Embodiment
[0063] Such as figure 1 As shown, a method for adjusting the pose of an aircraft component based on a 3-2-1 follow-up locator includes the following steps:
[0064] Step 1. Place the aircraft component 2 to be adjusted on three three-degree-of-freedom positioners 3a, two-degree-of-freedom positioners 3b, and single-degree-of-freedom positioners 3c through the ball joint type process joint;
[0065] Step 2: Set four measuring points 2a, 2b, 2c, and 2d on the aircraft component to be adjusted, and use the laser tracker 1 to measure each measuring point to obtain the actual measured coordinate X of each measuring point a 、X b 、X c and x d ;
[0066] Step 3, control system 4 according to the measured coordinate X of the measuring point a 、X b 、X c 、X d and target coordinates X ao 、X bo 、X co 、X do Calculate the difference between the current space attitude of the aircraft component to be adjusted and the target attitude, that is, the space attitude angle adjustments α,...
PUM
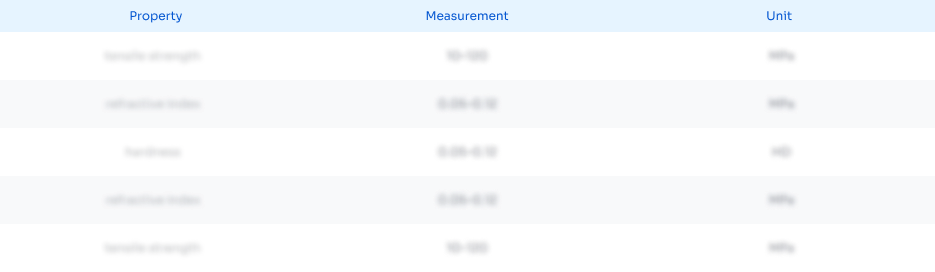
Abstract
Description
Claims
Application Information

- R&D
- Intellectual Property
- Life Sciences
- Materials
- Tech Scout
- Unparalleled Data Quality
- Higher Quality Content
- 60% Fewer Hallucinations
Browse by: Latest US Patents, China's latest patents, Technical Efficacy Thesaurus, Application Domain, Technology Topic, Popular Technical Reports.
© 2025 PatSnap. All rights reserved.Legal|Privacy policy|Modern Slavery Act Transparency Statement|Sitemap|About US| Contact US: help@patsnap.com