Multi-station automatic welding machine
An automatic welding machine and multi-station technology, applied in welding equipment, auxiliary welding equipment, welding/cutting auxiliary equipment, etc., can solve the problems of increased processing time and long clamping time of workpieces, etc.
- Summary
- Abstract
- Description
- Claims
- Application Information
AI Technical Summary
Problems solved by technology
Method used
Image
Examples
Embodiment Construction
[0010] The present invention is described in further detail below in conjunction with the embodiment that accompanying drawing provides.
[0011] see figure 1 , 2 , 3, a multi-station automatic welding machine includes a welding mechanism 1, a multi-station workbench mechanism 2 and a frame 3, the welding mechanism 1 is fixedly connected to the frame 3, and the welding mechanism 1 includes a column 1-1, Transmission screw 1-2, screw motor 1-3, guide column 1-4, cylinder device 1-5, rotating shaft device 1-6 and welding torch 1-7, screw motor 1-3 and transmission screw 1-2 Transmission connection, the column 1-1 has an inner cavity 1-1-1, the transmission screw rod 1-2 is located in the inner cavity 1-1-1, and the two ends are connected to the upper and lower two ends of the column 1-1 respectively , cylinder device 1-5 comprises cylinder 1-5-1, cylinder block 1-5-2 and cylinder guide post 1-5-3, and cylinder block 1-5-1 is connected with guide post 1-4 slidingly, and cylinde...
PUM
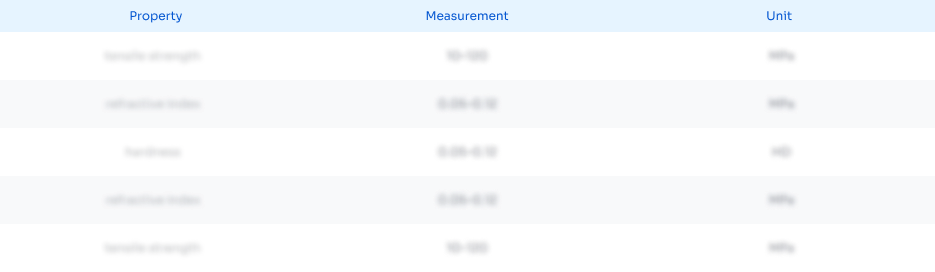
Abstract
Description
Claims
Application Information

- R&D
- Intellectual Property
- Life Sciences
- Materials
- Tech Scout
- Unparalleled Data Quality
- Higher Quality Content
- 60% Fewer Hallucinations
Browse by: Latest US Patents, China's latest patents, Technical Efficacy Thesaurus, Application Domain, Technology Topic, Popular Technical Reports.
© 2025 PatSnap. All rights reserved.Legal|Privacy policy|Modern Slavery Act Transparency Statement|Sitemap|About US| Contact US: help@patsnap.com