Spiral forced feed system
A technology of forced feeding and screwing, which is applied in the direction of mold extrusion granulation, etc., can solve the problems of low molding pressure, low production efficiency, and poor product quality, and achieve the goal of increasing extrusion pressure, increasing production efficiency, and improving product quality. Effect
- Summary
- Abstract
- Description
- Claims
- Application Information
AI Technical Summary
Problems solved by technology
Method used
Image
Examples
Embodiment Construction
[0013] The invention is a novel screw forced feeding system, which is mainly used in the technical field of roller extrusion granulation. The powdery material treated by the front end enters the lower hopper 5 through the feeding port on the lower hopper cover 3 . The variable frequency motor 1 drives the extrusion screw 6 to rotate through the adjustable connecting flange 4 to form extrusion on the material 10 .
[0014] see figure 1 , the concrete structure of the present invention is:
[0015] A screw forced feeding system, including a motor 1, a bearing seat 2, a lower hopper cover 3, a connecting flange 4, a lower hopper for storing materials 5, an extrusion screw 6, a support bracket 7, a vent cap 8 and an extrusion Pressure roller 9; Wherein,
[0016] The motor 1 is connected to the lower hopper cover 3 through the bearing seat 2, and drives the extrusion screw 6 to rotate through the connecting flange 4, so as to give a forced downward extrusion force to the materia...
PUM
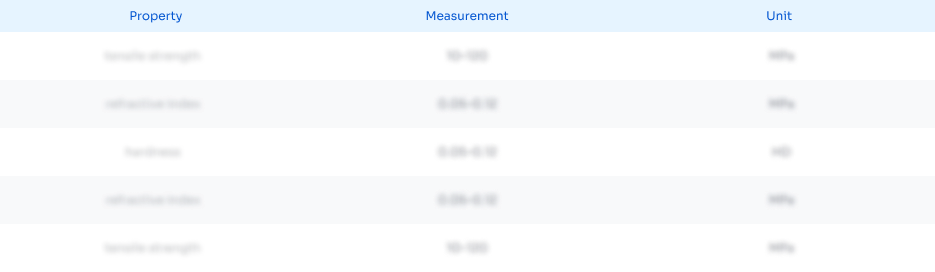
Abstract
Description
Claims
Application Information

- Generate Ideas
- Intellectual Property
- Life Sciences
- Materials
- Tech Scout
- Unparalleled Data Quality
- Higher Quality Content
- 60% Fewer Hallucinations
Browse by: Latest US Patents, China's latest patents, Technical Efficacy Thesaurus, Application Domain, Technology Topic, Popular Technical Reports.
© 2025 PatSnap. All rights reserved.Legal|Privacy policy|Modern Slavery Act Transparency Statement|Sitemap|About US| Contact US: help@patsnap.com