Method for reducing emission of carbon dioxide in catalytic cracking flue gas
A technology of carbon dioxide and catalytic cracking, which is only applied in the fields of refining and cracking process treatment in multi-stage series, petroleum industry, water treatment and refining, etc., can solve the problem of not fundamentally solving carbon dioxide emissions, reducing carbon dioxide emissions, unaccounted for carbon dioxide and other issues, to achieve good emulsification function and effect, reduce carbon dioxide emissions, and achieve remarkable results in economic and environmental benefits
- Summary
- Abstract
- Description
- Claims
- Application Information
AI Technical Summary
Problems solved by technology
Method used
Image
Examples
Embodiment 1
[0022] The multifunctional composite emulsifier is made by mixing 45% of Span 80, 45% of triethanolamine surfactant and 10% of light diesel oil co-solvent.
[0023] During production, the emulsified oil of FCC raw material was prepared under the conditions of water addition 8%, emulsifier addition 0.05%, emulsification temperature 75°C, stirring speed 20000r / min, and its properties are listed in Table 2.
[0024] The catalytic cracking test was carried out on the riser unit with FCC feedstock and emulsified feedstock respectively. The process conditions are: reaction temperature 505°C, regeneration temperature 700°C, agent-oil ratio 5.0. The test is continuous oil feeding for 10 hours, and the oil feeding amount is 8kg; the feeding method of the emulsified raw material is continuous feeding, a homogeneous emulsifying equipment is installed in front of the riser nozzle, the stirring speed is adjustable, and the emulsified oil processing capacity is 0-50L . The resulting oil i...
Embodiment 2
[0028] The multifunctional compound emulsifier is made by mixing 50% of Span 80, 35% of triethanolamine surfactant and 15% of light diesel co-solvent.
[0029] During production, FCC raw material emulsified oil was prepared under the conditions of 2% water addition, 0.01% emulsifier addition, emulsification temperature 45°C, and stirring speed 16000r / min. The oil property analysis is shown in Table 2.
[0030] The catalytic cracking test was carried out on the riser unit with FCC feedstock and emulsified feedstock respectively. The process conditions are: reaction temperature 505°C, regeneration temperature 700°C, agent-oil ratio 5.0. The test is continuous oil feeding for 10 hours, and the oil feeding amount is 8kg; the feeding method of the emulsified raw material is continuous feeding, a homogeneous emulsifying equipment is installed in front of the riser nozzle, the stirring speed is adjustable, and the emulsified oil processing capacity is 0-50L . The resulting oil is s...
Embodiment 3
[0034] The multifunctional composite emulsifier is made by mixing 50% of Span 80, 42% of triethanolamine surfactant and 8% of light diesel oil co-solvent.
[0035] During production, FCC raw material emulsified oil was prepared under the conditions of water addition of 10%, emulsifier addition of 2%, emulsification temperature of 90°C, and stirring speed of 18,000 r / min. The oil property analysis is shown in Table 2.
[0036] The catalytic cracking test was carried out on the riser unit with FCC feedstock and emulsified feedstock respectively. The process conditions are: reaction temperature 505°C, regeneration temperature 700°C, agent-oil ratio 5.0. The test is continuous oil feeding for 10 hours, and the oil feeding amount is 8kg; the emulsified raw material feeding method is continuous feeding, and a homogeneous emulsifying equipment is installed in front of the nozzle of the riser, the stirring speed is adjustable, and the emulsified oil processing capacity is 0-50L . The ...
PUM
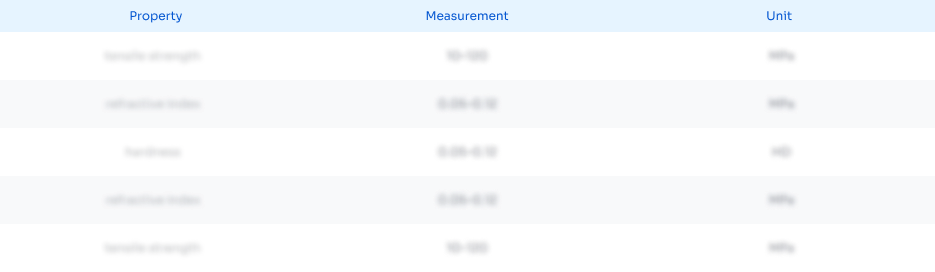
Abstract
Description
Claims
Application Information

- R&D Engineer
- R&D Manager
- IP Professional
- Industry Leading Data Capabilities
- Powerful AI technology
- Patent DNA Extraction
Browse by: Latest US Patents, China's latest patents, Technical Efficacy Thesaurus, Application Domain, Technology Topic, Popular Technical Reports.
© 2024 PatSnap. All rights reserved.Legal|Privacy policy|Modern Slavery Act Transparency Statement|Sitemap|About US| Contact US: help@patsnap.com