Lipophilic mineral composite fibers and preparation method thereof
A composite fiber and lipophilic technology, applied in glass manufacturing equipment, manufacturing tools, etc., can solve the problems of poor alkali resistance, strength and toughness degradation of glass fiber, etc., and achieve the effect of simple preparation method and easy access to raw materials
- Summary
- Abstract
- Description
- Claims
- Application Information
AI Technical Summary
Problems solved by technology
Method used
Image
Examples
Embodiment 1
[0036] (1) Raw material pretreatment: crush brucite and serpentinite with a crushing and ball milling machine to sort out the materials with a particle size of 80-90 mesh, and send them to the dust removal equipment for dust removal to obtain the fine materials required for production. Loosen and sieve to remove powdery mineral impurities to obtain crude mineral fiber;
[0037] (2) The crude mineral fiber is dried in a rotary temperature-controlled dryer, and the temperature of the dryer is controlled between 180°C and 240°C. After the material is dried, it is sent to the depolymerization machine for depolymerization. The linear speed of the depolymerization machine is 100-130m / s, so that the bundled fibers are depolymerized into monofilaments without destroying the aspect ratio;
[0038] (3) Chemically modify the fiber surface in the intermittent sub-storage surface modification equipment: inject the silicone penetrant into the buffer mixing tank with a high-pressure metering pump...
Embodiment 2
[0047] (1) Raw material pretreatment: crush brucite and serpentinite with a crushing and ball milling machine to sort out the materials with a particle size of 80-90 mesh, and send them to the dust removal equipment for dust removal to obtain the fine materials required for production. Loosen and sieve to remove powdery mineral impurities to obtain crude mineral fiber;
[0048] (2) The crude mineral fiber is dried in a rotary temperature-controlled dryer, and the temperature of the dryer is controlled between 180°C and 240°C. After the material is dried, it is sent to the depolymerization machine for depolymerization. The linear speed of the depolymerization machine is 100-130m / s, so that the bundled fibers are depolymerized into monofilaments without destroying the aspect ratio;
[0049] (3) Chemical modification of the fiber surface in the intermittent sub-storage surface modification equipment: the silicone penetrant is injected into the buffer mixing tank with a high-pressure m...
PUM
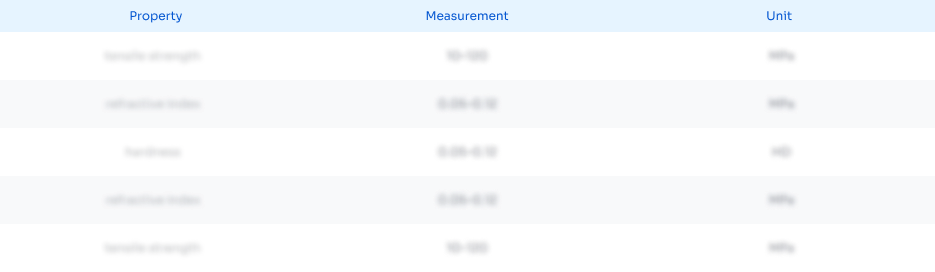
Abstract
Description
Claims
Application Information

- Generate Ideas
- Intellectual Property
- Life Sciences
- Materials
- Tech Scout
- Unparalleled Data Quality
- Higher Quality Content
- 60% Fewer Hallucinations
Browse by: Latest US Patents, China's latest patents, Technical Efficacy Thesaurus, Application Domain, Technology Topic, Popular Technical Reports.
© 2025 PatSnap. All rights reserved.Legal|Privacy policy|Modern Slavery Act Transparency Statement|Sitemap|About US| Contact US: help@patsnap.com