Method for modifying cellulose acetate butyrate (CAB) for electro-silvered simulating coating
A technology of acetic acid butyric acid and silver paint, applied in the direction of coating, can solve the problems of increasing the production cost of enterprises, the solvent resistance, hardness and other properties of the coating film are not significantly improved, and the production cost is high, and the solvent resistance performance and hardness can be achieved. Improved effects, less toxicity of reactants, and lower production costs
- Summary
- Abstract
- Description
- Claims
- Application Information
AI Technical Summary
Problems solved by technology
Method used
Image
Examples
Embodiment 1
[0044] Nitrogen was passed through the four-necked flask for 5 minutes, 340 parts of xylene was added into the container, and heated while stirring. When the temperature rose to 90°C, 100 parts of dry CAB-381-20 were added into the container (drying is the CAB-381-20 was dried in a vacuum drying oven for 12 hours, the oven temperature was 35°C), and the temperature continued to rise to keep the temperature constant at 145°C. After the CAB was completely dissolved, 28 parts of methyl acrylate and 8 parts of dibutyl A mixed solution of tin oxide and 127.5 parts of xylene was reacted at 145°C for 6 hours, then 267 parts of ethyl acetate and 167 parts of ethylene glycol butyl ether were added, and after the temperature was lowered to 95°C, the following mixture was added dropwise: 167 Parts of methyl methacrylate, 167 parts of ethyl acetate, 100 parts of ethylene glycol butyl ether, 5 parts of dibenzoyl peroxide, and drop them in about 2 hours, and react for 3 hours to get methyl m...
Embodiment 2
[0046]Nitrogen was passed through the container for 5 minutes, and 340 parts of methyl ethyl ketone was added into the container, and heated while stirring. When the temperature rose to 90°C, 100 parts of dry CAB-381-20 were added into the container (drying means CAB- 381-20 was dried in a vacuum drying oven for 4 hours, the oven temperature was 100°C), and the temperature continued to rise to keep the temperature constant at 145°C. After the CAB was completely dissolved, 41 parts of butyl acrylate and 8 parts of triethyltin oxide were added And a mixed solution of 127.5 parts of xylene, after reacting at 145°C for 6 hours, add 267 parts of ethyl acetate and 167 parts of butyl acetate, after lowering the temperature to 95°C, start to drop the following mixture: 167 parts of methacrylic acid Methyl ester, 167 parts of ethyl acetate, 100 parts of ethylene glycol butyl ether, and 5 parts of dibenzoyl peroxide were added dropwise in about 2 hours, and the grafted modified methyl me...
Embodiment 3
[0048] Nitrogen was passed through the container for 5 minutes, and 340 parts of xylene was added into the container, and heated while stirring. When the temperature rose to 90°C, 100 parts of dry CAB-551-0.2 were added to the container, and the temperature continued to rise. Constant at 145°C, after the CAB is completely dissolved, add a mixed solution of 45.3 parts of butyl methacrylate, 8 parts of diethyl tin oxide and 127.5 parts of xylene, react at 145°C for 6 hours, then add 267 parts of acetic acid Ethyl ester and 167 parts of acetone, after lowering the temperature to 95°C, start to add the following mixture dropwise: 167 parts of methyl methacrylate, 167 parts of acetone, 100 parts of ethylene glycol butyl ether, 5 parts of dibenzoyl peroxide, The dropwise addition was completed in about 2 hours, and the methyl methacrylate graft-modified CAB was obtained after 3 hours of reaction. Infrared test was carried out after the CAB of butyl methacrylate transesterification g...
PUM
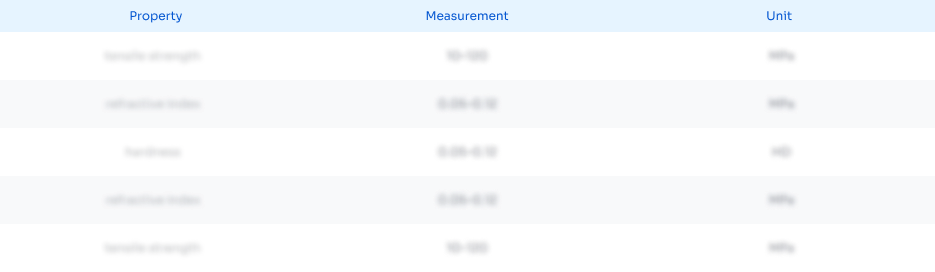
Abstract
Description
Claims
Application Information

- R&D
- Intellectual Property
- Life Sciences
- Materials
- Tech Scout
- Unparalleled Data Quality
- Higher Quality Content
- 60% Fewer Hallucinations
Browse by: Latest US Patents, China's latest patents, Technical Efficacy Thesaurus, Application Domain, Technology Topic, Popular Technical Reports.
© 2025 PatSnap. All rights reserved.Legal|Privacy policy|Modern Slavery Act Transparency Statement|Sitemap|About US| Contact US: help@patsnap.com