Method for treating purification copper-removing slag of nickel electrolysis anode solution
A technology of anolyte and nickel electrolysis, which is applied in the field of copper-nickel hydrometallurgy, can solve the problems of low copper-nickel ratio, and achieve the effect of easy control and operation, and easy operation
- Summary
- Abstract
- Description
- Claims
- Application Information
AI Technical Summary
Problems solved by technology
Method used
Examples
Embodiment 1
[0054] First adjust the pH value of the nickel electrolysis anolyte to 4; add excess nickel thiocarbonate to react with the copper in the solution, control the reaction temperature to 90° C., and the reaction time to 60 minutes to obtain copper removal slag. Add 10Kg of copper removal slag with a copper-nickel ratio of 0.5 to 84 liters of CuSO with a pH of 5.0 and a copper concentration of 80g / L 4 In the solution, the molar ratio of nickel in the copper-removing slag to copper in the copper-containing solution is 0.7, and the reaction temperature is controlled at 25° C. After 120 minutes of reaction, the copper-nickel ratio of 151 is separated to obtain the copper-removing slag, and the nickel concentration is 52.7g / L, NiSO with a copper concentration of 0.33g / L 4 solution. Then 5.8Kg of Na 2 Dissolve S in 70L of water first, then add 4.7L of CS 2 solution, after 10 hours of reaction, 74mol of Na 2 CS 3 solution. with NiSO 4 Solution reaction to prepare nickel thiocarb...
Embodiment 2
[0056] Decopper slag produces with embodiment 1, and the copper removal slag that 10Kg copper-nickel ratio is 1 is added to 80 liters of pH is 7.0, and copper concentration is 60g / L to contain CuSO 4 and Cu 2 SO 4 In the mixed solution, the molar ratio of nickel in the copper-removing slag to copper in the copper-containing solution is 0.8, and the controlled reaction temperature is 50°C. After 80 minutes of reaction, the copper-nickel ratio of 200 is separated to obtain the copper-removing slag, and the nickel concentration is 34.6g / L, NiSO with a copper concentration of 0.002g / L 4 solution. Then 3.58Kg of Na 2 Dissolve S in 50L of water first, then add 5.55L of CS 2 solution, after 10 hours of reaction, 46mol of Na 2 C 2 S 5 solution. with NiSO 4 Solution reaction to prepare nickel thiocarbonate; then react with nickel electrolytic anolyte containing 43mol copper and pH 4.2 at 20°C to remove copper. After copper removal, the copper concentration is 1.1mg / L, and the ...
Embodiment 3
[0058] Decopper slag produces with embodiment 1, and 10Kg copper-nickel ratio is the copper removal slag of 1.5 and joins 54 liters of pH and is 2.5, and copper concentration is the CuCl of 52g / L 2 In the solution, the molar ratio of nickel in the copper-removing slag to copper in the copper-containing solution is 1.0, and the reaction temperature is controlled at 90°C. After 60 minutes of reaction, the copper-nickel ratio of 178 is separated to obtain the copper-removing slag, and the nickel concentration is 36.9g / L, NiCl with a copper concentration of 0.67g / L 2 solution. Then 3.63Kg of K 2 Dissolve S in 50L of water first, then add 3.98L of CS 2 solution, after 20 hours of reaction, 33mol of K 2 C 2 S 5 solution. with NiCl 2 Solution reaction to prepare nickel thiocarbonate; then react with nickel electrolytic anolyte containing 32mol copper and pH 6.0 at 90°C to remove copper. After copper removal, the copper concentration is 0.98 mg / L, and the copper-nickel ratio i...
PUM
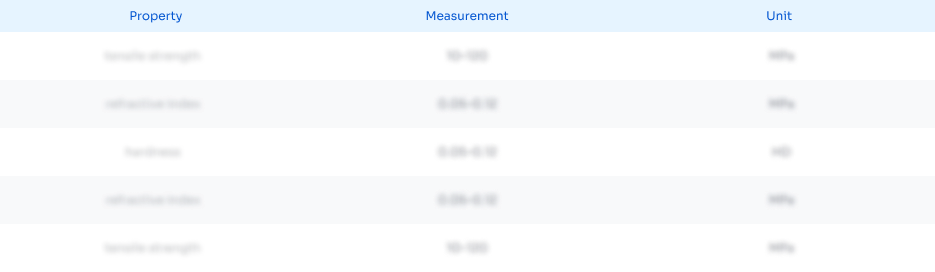
Abstract
Description
Claims
Application Information

- Generate Ideas
- Intellectual Property
- Life Sciences
- Materials
- Tech Scout
- Unparalleled Data Quality
- Higher Quality Content
- 60% Fewer Hallucinations
Browse by: Latest US Patents, China's latest patents, Technical Efficacy Thesaurus, Application Domain, Technology Topic, Popular Technical Reports.
© 2025 PatSnap. All rights reserved.Legal|Privacy policy|Modern Slavery Act Transparency Statement|Sitemap|About US| Contact US: help@patsnap.com