Gear crack propagation simulated wavelet extension finite element simulation analysis method
A technology of extended finite element and crack extension, applied in the field of finite element analysis, can solve problems such as low efficiency, discontinuity, and inability to jump material properties, and achieve the effect of high calculation efficiency and high calculation accuracy
- Summary
- Abstract
- Description
- Claims
- Application Information
AI Technical Summary
Problems solved by technology
Method used
Image
Examples
Embodiment Construction
[0057] The present invention will be further described below in conjunction with the accompanying drawings and examples.
[0058] Such as figure 2 Shown is a schematic diagram of the workflow of this embodiment. It mainly consists of 3 parts, and the detailed steps are as follows.
[0059] 1. Use Pro / E drawing software to draw a meshing model of a gear with a modulus of 2 and a number of teeth of 19 and another large gear, such as image 3 shown. According to the requirements, any form of crack fault can be added to the gear teeth, and the position, size, shape and other characteristics of the crack can be changed to simulate complex crack faults that are more in line with the actual situation. Figure 4 Shown is a hypothetical tooth with an illustrated crack failure at the root.
[0060] 2. Use ABAQUS to divide the finite element grid and output the grid node coordinates:
[0061] 1) Import the gear model drawn by Pro / E into ABAQUS and divide it to generate a gear model...
PUM
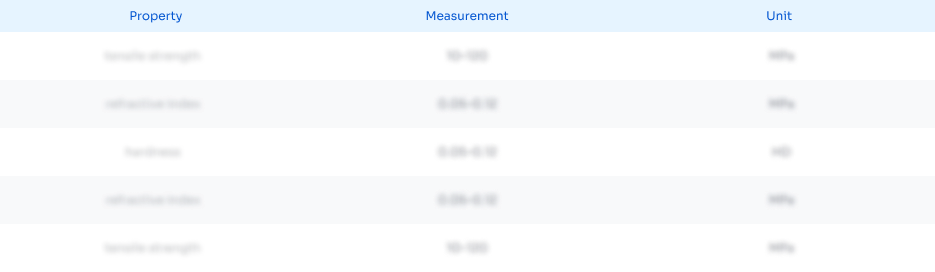
Abstract
Description
Claims
Application Information

- R&D
- Intellectual Property
- Life Sciences
- Materials
- Tech Scout
- Unparalleled Data Quality
- Higher Quality Content
- 60% Fewer Hallucinations
Browse by: Latest US Patents, China's latest patents, Technical Efficacy Thesaurus, Application Domain, Technology Topic, Popular Technical Reports.
© 2025 PatSnap. All rights reserved.Legal|Privacy policy|Modern Slavery Act Transparency Statement|Sitemap|About US| Contact US: help@patsnap.com