Method for preparing tobacco sheets through tobacco waste materials by papermaking method
A technology for tobacco sheets and wastes, which is applied in the field of preparing tobacco sheets by using tobacco material wastes by a papermaking method, can solve the problems of high fine fiber content, difficulty in material concentration, and high content of miscellaneous cells, so as to enhance the effect of fine fiberization and improve the Physical properties, the effect of improving retention
- Summary
- Abstract
- Description
- Claims
- Application Information
AI Technical Summary
Problems solved by technology
Method used
Examples
Embodiment 1
[0029] (1) Mix 500Kg of washed tobacco stems and 300Kg of shredded tobacco leaves, soak in 4000Kg of water at 20°C for 3 hours, extract, and separate the solid and liquid to obtain a solid-phase mixture and extract; put 200Kg of tobacco powder at a temperature of 600Kg Soak in water at 80°C for 1 hour, extract, and separate solid phase to obtain solid phase tobacco powder and extract;
[0030] (2) Adjust the solid-phase mixture to a concentration of 15%, and transport it to a high-consistency refiner for flaking. After flaking, the beating degree of the material is 10oSR;
[0031] (3) Adjust the mass concentration of the decomposed material to 12%, and transport it to a medium-consistency refiner for beating treatment. During the beating process, adjust the pressure of the grinding zone formed between the grinding plates to 0.3MPa. After the medium-concentration beating treatment, the beating degree of the pulp is 20oSR, which becomes the pulp for the paper machine to make tob...
Embodiment 2
[0037] (1) Mix 400Kg of washed tobacco stems and 300Kg of shredded tobacco leaves, soak in 4900Kg of water at a temperature of 35°C for 1 hour, extract, and separate the solid and liquid to obtain a solid-phase mixture and an extract; Soak in water at 40°C for 3 hours, extract, and separate solid phase to obtain solid phase tobacco powder and extract;
[0038] (2) Adjust the solid-phase mixture to a concentration of 30%, and transport it to a high-consistency refiner for flaking, and the beating degree of the material after flaking is 15oSR;
[0039] (3) Adjust the high-consistency decomposed material to a concentration of 6%, and transport it to a medium-consistency refiner for beating treatment. During the beating process, adjust the pressure of the grinding zone formed between the grinding plates to 0.6MPa. The pulp after medium-concentration beating treatment has a beating degree of 30oSR, which can be used for making tobacco sheets by paper machines;
[0040] (4) Mix the...
Embodiment 3
[0045] (1) Mix 400Kg of washed tobacco stems and 200Kg of crushed tobacco leaves, soak in 3000Kg of water at a temperature of 30°C for 2 hours, extract, and separate the solid and liquid to obtain a solid-phase mixture and an extract; put 400Kg of tobacco powder at 2000Kg Soak in water at 60°C for 2 hours, extract, and separate solid phase to obtain solid phase tobacco powder and extract;
[0046] (2) Adjust the solid-phase mixture obtained after extraction to a concentration of 23%, and transport it to a high-consistency refiner for decompression. After decompression, the beating degree of the material is 12oSR;
[0047] (3) Adjust the high-consistency decomposed material to a concentration of 9%, and transport it to a medium-consistency refiner for beating treatment. During the beating process, adjust the pressure of the grinding zone formed between the grinding plates to 0.4MPa. The beating degree of the pulp after the medium-consistency beating treatment is 26oSR, which be...
PUM
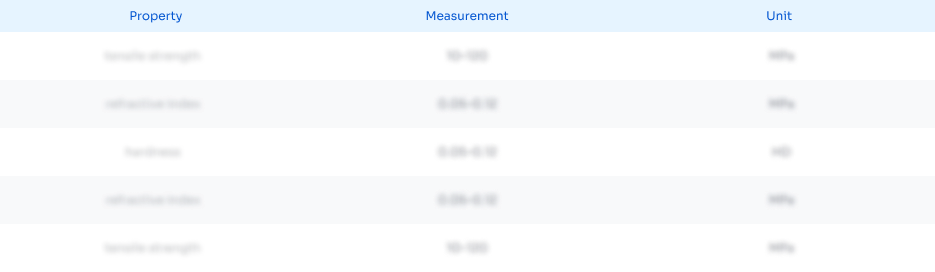
Abstract
Description
Claims
Application Information

- R&D
- Intellectual Property
- Life Sciences
- Materials
- Tech Scout
- Unparalleled Data Quality
- Higher Quality Content
- 60% Fewer Hallucinations
Browse by: Latest US Patents, China's latest patents, Technical Efficacy Thesaurus, Application Domain, Technology Topic, Popular Technical Reports.
© 2025 PatSnap. All rights reserved.Legal|Privacy policy|Modern Slavery Act Transparency Statement|Sitemap|About US| Contact US: help@patsnap.com