Two-axis gyroscope with piezo-driven capacitive sensing
A technology of capacitance detection and two-axis gyroscope, which is applied in the field of micro gyroscope, can solve the problems of gyroscope performance influence, stress concentration, and small effective vibration amplitude, etc., and achieve the effect of easy processing technology, strong impact resistance and high reliability
- Summary
- Abstract
- Description
- Claims
- Application Information
AI Technical Summary
Problems solved by technology
Method used
Image
Examples
Embodiment Construction
[0026] A preferred embodiment of the present invention will be described in detail below in conjunction with the accompanying drawings: this embodiment is implemented on the premise of the technical solution of the present invention, and detailed implementation methods and specific operating procedures are provided, but the protection scope of the present invention does not Limited to the following examples.
[0027] Such as figure 1 , figure 2 , image 3 As shown, this embodiment includes a gyro vibrator 1 , a support cylinder 2 , a piezoelectric film drive electrode 3 , an upper plate signal detection electrode 4 , a lower plate signal detection electrode 5 , an upper plate 6 , and a lower plate 7 .
[0028] The material of the gyro vibrator 1 is a metal material, and the structure is disc-shaped. One end of the disc-shaped gyro vibrator 1 is the upper surface, and the surface parallel to the other end is the lower surface.
[0029] The support cylinder 2 is m...
PUM
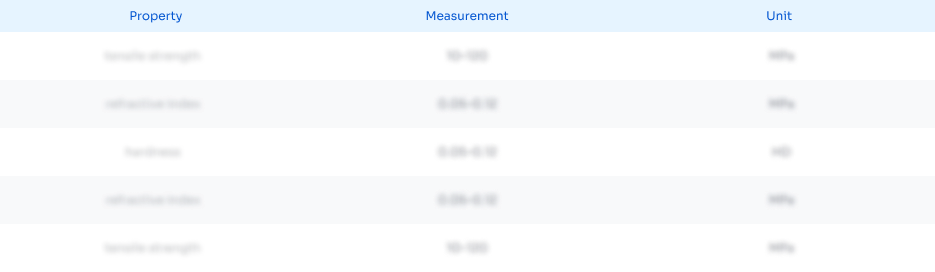
Abstract
Description
Claims
Application Information

- R&D
- Intellectual Property
- Life Sciences
- Materials
- Tech Scout
- Unparalleled Data Quality
- Higher Quality Content
- 60% Fewer Hallucinations
Browse by: Latest US Patents, China's latest patents, Technical Efficacy Thesaurus, Application Domain, Technology Topic, Popular Technical Reports.
© 2025 PatSnap. All rights reserved.Legal|Privacy policy|Modern Slavery Act Transparency Statement|Sitemap|About US| Contact US: help@patsnap.com