Special core support for sand box for large engine cylinder block
A technology for engine cylinder block and sand box, which is applied to mold boxes, casting equipment, metal processing equipment, etc., can solve the problems of poor deformation prevention effect of sand core, insufficient rigidity and strength of core support, deformation of sand core due to heat, etc. Broad market application prospects, ensuring multi-directional positioning, and the effect of simple core support structure
- Summary
- Abstract
- Description
- Claims
- Application Information
AI Technical Summary
Problems solved by technology
Method used
Image
Examples
Embodiment Construction
[0016] Below in conjunction with accompanying drawing, the present invention will be further explained:
[0017] refer to figure 1 and figure 2 , the present invention includes four dumbbell-shaped pillars (upper right pillar 2, lower right pillar 3, lower left pillar 4 and upper left pillar 5) installed on two side plates 1.1 of saddle-shaped bottom plate 1, each side has 2 pillars respectively, Corresponding to the installation, the height of the pillar H=(0.6-0.9)×the wall thickness of the same side of the sand box; the minimum diameter of the middle section of the pillar is D=(0.2-0.5)×the diameter of the hot spot, and the two ends of the pillar (i.e. dumbbell shape The maximum diameter of the two ends) is 1.5-2 times the minimum diameter. The distance between the pillars on the same side is L=(0.2-0.5)×the sand core height H1. see figure 1 , in this embodiment, because the wall thicknesses of the sand boxes corresponding to the pillars on the two side plates 1.1 are ...
PUM
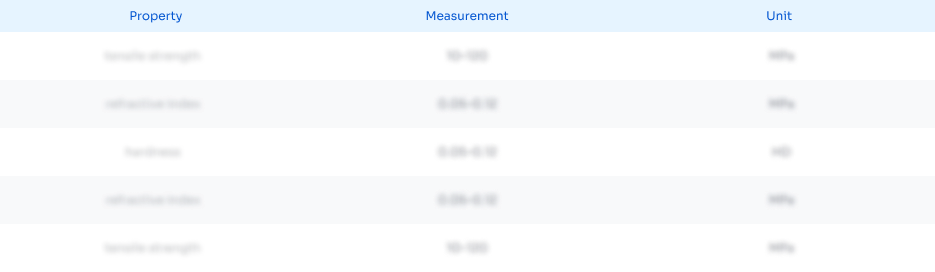
Abstract
Description
Claims
Application Information

- R&D
- Intellectual Property
- Life Sciences
- Materials
- Tech Scout
- Unparalleled Data Quality
- Higher Quality Content
- 60% Fewer Hallucinations
Browse by: Latest US Patents, China's latest patents, Technical Efficacy Thesaurus, Application Domain, Technology Topic, Popular Technical Reports.
© 2025 PatSnap. All rights reserved.Legal|Privacy policy|Modern Slavery Act Transparency Statement|Sitemap|About US| Contact US: help@patsnap.com