3D Pose Measurement Method of Object Based on Geometric Constraints
A technology of 3D attitude and geometric constraints, which is applied in the field of 3D attitude measurement of objects based on geometric constraints, and can solve problems such as special requirements for the geometric shape of feature points, a large number of feature points for pose calculation, and complex calculation processes, etc.
- Summary
- Abstract
- Description
- Claims
- Application Information
AI Technical Summary
Problems solved by technology
Method used
Image
Examples
Embodiment Construction
[0035] measurement system such as figure 1 As shown, the system consists of a sigma two-dimensional turntable, two cameras, and a target for measurement. The camera is fixed on the support frame and the position of the camera is adjusted according to the height of the turntable. The measurement target is a cube except the bottom surface. There are 4 non-coplanar infrared LEDs on each plane as the positioning feature points. The two-dimensional turntable drives the target to deflect. , Pitch two degrees of freedom movement, when using a single camera to shoot positioning feature points for pose calculation, in order to avoid the blind area of shooting, but also to achieve the calibration of the two-dimensional turntable rotation axis, two cameras can be used from different angles Shoot location markers. The computer sends signals to the control box of the turntable through the serial port to control the movement of the turntable.
[0036] The coordinates of feature points i...
PUM
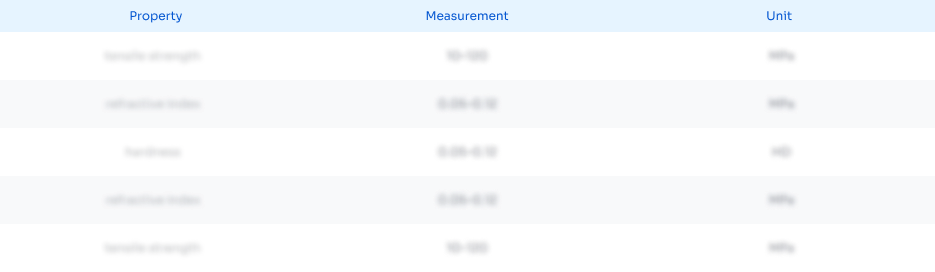
Abstract
Description
Claims
Application Information

- R&D Engineer
- R&D Manager
- IP Professional
- Industry Leading Data Capabilities
- Powerful AI technology
- Patent DNA Extraction
Browse by: Latest US Patents, China's latest patents, Technical Efficacy Thesaurus, Application Domain, Technology Topic, Popular Technical Reports.
© 2024 PatSnap. All rights reserved.Legal|Privacy policy|Modern Slavery Act Transparency Statement|Sitemap|About US| Contact US: help@patsnap.com