Direct heat setting method and device for two-for-one twisting
A technology of heat setting and heat setting, which is applied in the direction of textiles and paper making, and can solve the problems of easy bruising of winding bobbins, uneven heat setting, long process route, etc., achieve good consistency, reduce back and forth handling, and short process flow Effect
- Summary
- Abstract
- Description
- Claims
- Application Information
AI Technical Summary
Problems solved by technology
Method used
Image
Examples
Embodiment 1
[0033] like image 3 A double-twisting direct heat-setting device is shown, the motor 9 is mounted on the frame 7, the dragon belt 8 is linked with the motor 9, the double-twisting spindle 6 is linked with the dragon belt 8, and a double-twisting spindle 6 is provided above. The biphenyl heating and setting box 5 is installed, and the winding mechanism 2 is installed above the biphenyl heating and setting box 5 , and the gear box 1 is linked with the winding mechanism 2 . An overfeeding roller 3 is provided between the biphenyl heating and setting box 5 and the double twisting spindle 6, and between the biphenyl heating and setting box 5 and the winding mechanism 2, respectively.
[0034] During operation, the motor 9 drives the belt 8 to move, and the belt 8 drives the double-twisting spindle 6 to rotate, completing the double-twisting and twisting of the twisted yarn 4. The twisted yarn 4 passes through the overfeeding roller 3, adjusts the tension and enters the heat settin...
Embodiment 2
[0036] like figure 1 As shown, the basic structure is the same as that of Embodiment 1, the difference is that one overfeeding roller 3 is provided, that is, one overfeeding roller 3 is provided between the biphenyl heating and setting box 5 and the winding mechanism 2, and the setting in the biphenyl heating The overfeed roller between the setting box 5 and the double twisting spindle 6, in this way, the twisted yarn 4 directly enters the heat setting box 5 for heat setting after being twisted from the double twisting spindle 6. Other procedures are the same as in Example 1.
Embodiment 3
[0038] like figure 2 As shown, the basic structure is the same as that of Embodiment 1, the difference is that the overfeed roller 3 is set to one, that is, an overfeed roller is provided between the biphenyl heating and setting box 5 and the double twisting spindle 6, and the setting in the biphenyl heating setting box 6 is cancelled. The overfeeding roller 3 between the box 5 and the winding mechanism 2, after the twisted yarn is twisted by 4 times, after the tension is adjusted by the overfeeding roller 3, it enters the heat setting box 5 for heat setting, and the twisted yarn 4 is heated from the heat setting. After the box 5 comes out, it directly enters the winding mechanism and is wound into a forming bobbin.
PUM
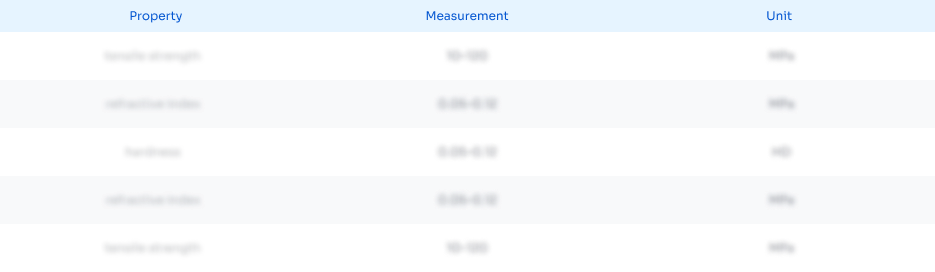
Abstract
Description
Claims
Application Information

- R&D
- Intellectual Property
- Life Sciences
- Materials
- Tech Scout
- Unparalleled Data Quality
- Higher Quality Content
- 60% Fewer Hallucinations
Browse by: Latest US Patents, China's latest patents, Technical Efficacy Thesaurus, Application Domain, Technology Topic, Popular Technical Reports.
© 2025 PatSnap. All rights reserved.Legal|Privacy policy|Modern Slavery Act Transparency Statement|Sitemap|About US| Contact US: help@patsnap.com