Radiating unit of directly-heated type electric heater and manufacturing method of radiating unit
A technology for a heat dissipation unit and an electric heater, applied in the field of electric heaters, can solve the problems of material waste cost, different degrees of close contact of the structure and dimensions, and the heat dissipation unit affecting the heat transfer effect, etc., so as to avoid material waste and a simple manufacturing method. Effect
- Summary
- Abstract
- Description
- Claims
- Application Information
AI Technical Summary
Problems solved by technology
Method used
Image
Examples
Embodiment Construction
[0027] The present invention will be further described below in conjunction with the embodiments and the accompanying drawings.
[0028] like figure 1 , 2 In the embodiment of the heat dissipation unit shown, the heat dissipation profile 1 is provided with a rectangular core tube 1-1, and the core tube is provided with a rod-shaped electric heating core 2, and the rod-shaped electric heating core is composed of an insulator, a spiral electric heating wire and a high temperature resistant sheath lead wire, The spiral heating wire 6 is reciprocally distributed in the insulator along the long axis direction of the insulator ( figure 1 shown in dashed lines). The insulator is also provided with a connecting portion where the spiral heating wire 6 and the lead wire 5 of the high temperature resistant sheath are connected by a metal connection sleeve 7 . The insulator is composed of bonded and solidified magnesia sand, the insulator and the core tube are filled with magnesia sand...
PUM
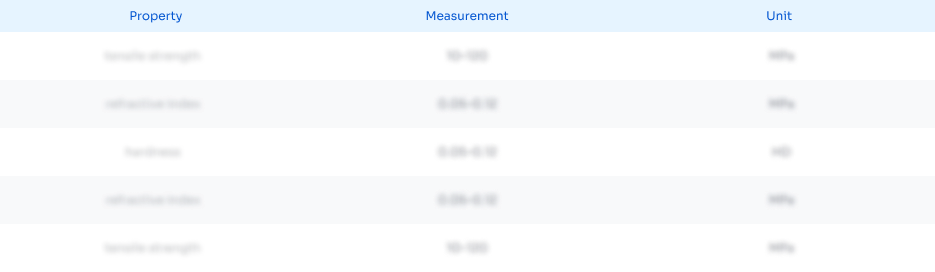
Abstract
Description
Claims
Application Information

- R&D Engineer
- R&D Manager
- IP Professional
- Industry Leading Data Capabilities
- Powerful AI technology
- Patent DNA Extraction
Browse by: Latest US Patents, China's latest patents, Technical Efficacy Thesaurus, Application Domain, Technology Topic, Popular Technical Reports.
© 2024 PatSnap. All rights reserved.Legal|Privacy policy|Modern Slavery Act Transparency Statement|Sitemap|About US| Contact US: help@patsnap.com