Multiple-spindle ratchet wheel strain testing system and method of pipe bend
A strain testing and testing system technology, applied in the direction of applying stable tension/pressure to test the strength of materials, measuring devices, instruments, etc., can solve the problems of insufficient data acquisition accuracy, inaccurate test position positioning, single loading type, etc. Achieve the effect of flexible test position, wide range of load conditions and applications, accurate and reliable data
- Summary
- Abstract
- Description
- Claims
- Application Information
AI Technical Summary
Problems solved by technology
Method used
Image
Examples
Embodiment Construction
[0034] The invention realizes the cyclic bending of the internal pressure pipe fittings by using a multi-axis fatigue testing machine with a jig auxiliary mechanism, and uses precision strain gauges to measure the ratchet strain of the elbow sample. The instruments used in this test method include design elbow specimen 5, multi-axis fatigue testing machine 11, multi-channel dynamic strain measuring instrument 6 and other auxiliary mechanisms. The design elbow sample 5 is mainly composed of three parts, one is a 90-degree elbow, and the other is straight sleeves (14) and (16) each with a length of 0.1 m, wherein the straight sleeve (16) has a side opening Through hole, and be connected with tee joint (17) weld seam, be used as exhaust hole; The third is two straight pipe pipe plugs (12) and (19) that each length is 0.1m; Pipe plug (12) and ( 19) It is connected with the straight sleeves (14) and (16) by butt welds; one of the pipe plugs (12) is designed with a threaded through ...
PUM
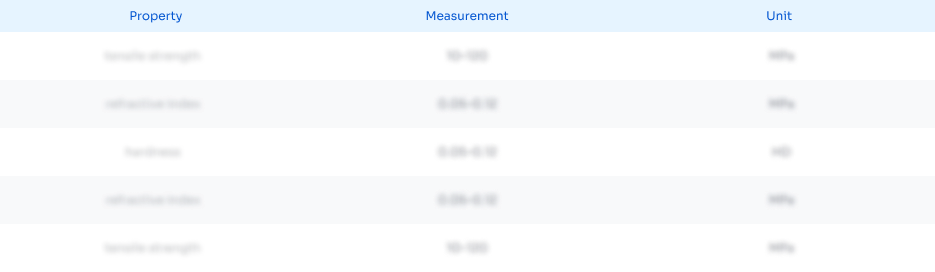
Abstract
Description
Claims
Application Information

- R&D
- Intellectual Property
- Life Sciences
- Materials
- Tech Scout
- Unparalleled Data Quality
- Higher Quality Content
- 60% Fewer Hallucinations
Browse by: Latest US Patents, China's latest patents, Technical Efficacy Thesaurus, Application Domain, Technology Topic, Popular Technical Reports.
© 2025 PatSnap. All rights reserved.Legal|Privacy policy|Modern Slavery Act Transparency Statement|Sitemap|About US| Contact US: help@patsnap.com