Device and method for measuring spatial free attitude of rigid object, and method for analyzing data
An object space and measuring device technology, which is applied to measuring devices, optical devices, static/dynamic balance tests, etc., can solve problems such as low measurement accuracy, complex instrument structure, and inability to meet simultaneous measurements, and achieve high measurement accuracy, The effect of simplifying the measuring device
- Summary
- Abstract
- Description
- Claims
- Application Information
AI Technical Summary
Problems solved by technology
Method used
Image
Examples
Embodiment Construction
[0030] see Figure 1~3 .
[0031] The cross indicates the generation of ray 5: at image 3 In , the laser beam generated by the laser 3 is input into the optical system through the transmission fiber 4 . First, the beam splitting prism 15 is divided into two mutually perpendicular laser beams, one of which is expanded by the beam expander 17 into a laser beam with a required width, and then focused by the corresponding cylindrical mirror 19 into linear light rays in the vertical direction. After being output by the dichroic prism group 18 and the reflector, the linear light in the vertical direction in the four directions in the plane is obtained. Secondly, the laser beam in another direction is expanded by a beam expander (not shown in the figure), and then focused into a linear line of light in the horizontal direction by a corresponding cylindrical mirror (not shown in the figure), which is reflected The mirror 16 is input to the dichroic prism group 18 for light synthes...
PUM
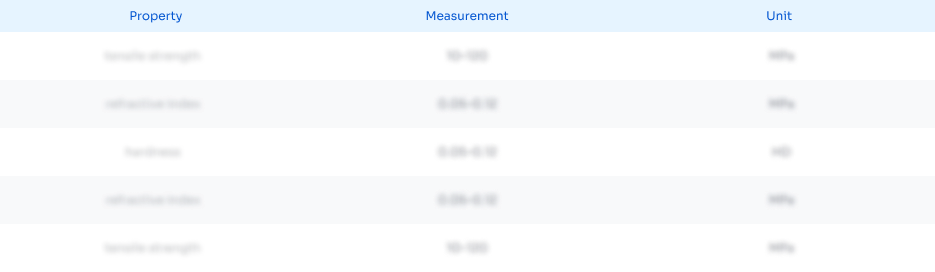
Abstract
Description
Claims
Application Information

- R&D
- Intellectual Property
- Life Sciences
- Materials
- Tech Scout
- Unparalleled Data Quality
- Higher Quality Content
- 60% Fewer Hallucinations
Browse by: Latest US Patents, China's latest patents, Technical Efficacy Thesaurus, Application Domain, Technology Topic, Popular Technical Reports.
© 2025 PatSnap. All rights reserved.Legal|Privacy policy|Modern Slavery Act Transparency Statement|Sitemap|About US| Contact US: help@patsnap.com