System for fully automatically reconstructing foot-type three-dimensional surface from a plurality of images captured by a plurality of cameras simultaneously
A three-dimensional surface, fully automatic technology, applied in image data processing, 3D modeling, foot or shoe last measurement devices, etc., can solve the problems of slow speed, difficult processing, low precision, etc. Effect
- Summary
- Abstract
- Description
- Claims
- Application Information
AI Technical Summary
Problems solved by technology
Method used
Image
Examples
Embodiment Construction
[0073] The implementation of the present invention to fully automatically reconstruct the three-dimensional surface of the foot shape from multiple images captured by multiple cameras at the same time, the process is as follows figure 1 shown, including the following seven steps:
[0074] 1. Generate the shoe last statistical deformation model: select the shoe last sample, form the shoe last sample set, design the mark points, generate the statistical deformation model, obtain the mark points of the samples to generate a point distribution model, and then proceed from the point distribution model set of the sample set Principal component analysis generates a statistical deformation model of the shoe last.
[0075] 1.1) Select a shoe last sample to form a shoe last sample set. The selection of the shoe last sample set has an important impact on the statistical deformation model generated later, and thus affects the accuracy of the initial estimation model of the foot shape. D...
PUM
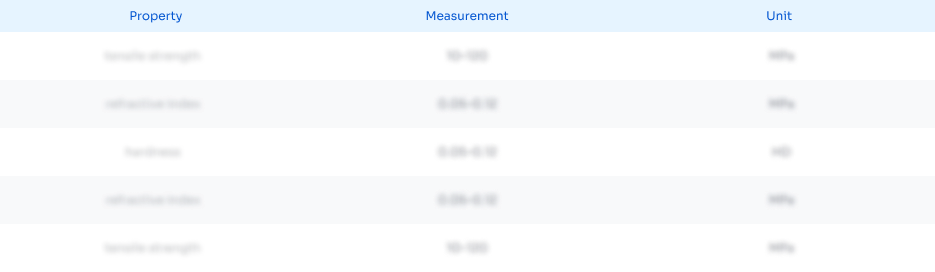
Abstract
Description
Claims
Application Information

- Generate Ideas
- Intellectual Property
- Life Sciences
- Materials
- Tech Scout
- Unparalleled Data Quality
- Higher Quality Content
- 60% Fewer Hallucinations
Browse by: Latest US Patents, China's latest patents, Technical Efficacy Thesaurus, Application Domain, Technology Topic, Popular Technical Reports.
© 2025 PatSnap. All rights reserved.Legal|Privacy policy|Modern Slavery Act Transparency Statement|Sitemap|About US| Contact US: help@patsnap.com