Cast aluminium rotor punching
A cast aluminum rotor and punching technology, applied to the magnetic circuit rotating parts, magnetic circuit shape/style/structure, etc., can solve the problems of different iron core lengths, inconvenient production management, long production cycle, etc., to reduce production Cost, simple structure, easy to achieve effect
- Summary
- Abstract
- Description
- Claims
- Application Information
AI Technical Summary
Problems solved by technology
Method used
Image
Examples
Embodiment Construction
[0014] Please refer to figure 1 and figure 2 as shown, figure 1 It is a structural schematic diagram of punching a cast aluminum rotor of the present invention; figure 2 for figure 1 Partial enlarged view of A in the center.
[0015] In this embodiment, a cast aluminum rotor punch includes a punch body 1, a shaft hole 2 is opened at the center of the punch body 1, a keyway 3 is opened on the shaft hole 2, and the There are 84 grooves 4 on the radial surface near the periphery of the punching body 1. The grooves 4 adopt a closed groove structure, and the distance between the groove-shaped outer groove 5 and the periphery 6 of the punching body is smaller than the length of the air gap. 0.2mm-0.4mm, the air gap length H is 1.4mm, then the distance between the groove-shaped outer groove 5 and the periphery 6 of the punch body is 1.0mm-1.2mm.
[0016] The groove shape of the above-mentioned cast aluminum rotor punch adopts a closed groove structure. When the rotor is cast a...
PUM
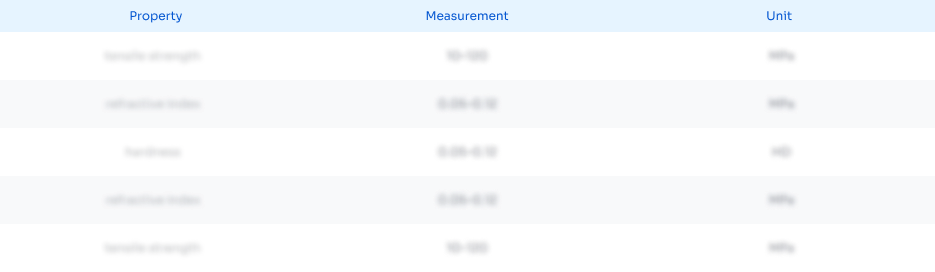
Abstract
Description
Claims
Application Information

- R&D
- Intellectual Property
- Life Sciences
- Materials
- Tech Scout
- Unparalleled Data Quality
- Higher Quality Content
- 60% Fewer Hallucinations
Browse by: Latest US Patents, China's latest patents, Technical Efficacy Thesaurus, Application Domain, Technology Topic, Popular Technical Reports.
© 2025 PatSnap. All rights reserved.Legal|Privacy policy|Modern Slavery Act Transparency Statement|Sitemap|About US| Contact US: help@patsnap.com