Piezoelectric valve
A valve and piezoelectric technology, applied in the direction of valve details, valve devices, valve operation/release devices, etc., can solve the problems of insufficient control accuracy, small flow rate, low temperature resistance, etc., to reduce volume and quality, and structure compact effect
- Summary
- Abstract
- Description
- Claims
- Application Information
AI Technical Summary
Problems solved by technology
Method used
Image
Examples
Embodiment Construction
[0050] The present invention will be further described in detail below in conjunction with the accompanying drawings and embodiments.
[0051] The piezoelectric valve designed by the present invention adopts a micro-manufacturing process to manufacture the key sealing parts spool 410 and valve seat 411 in the valve body assembly 4, and the rest of the valve body assembly 4 is manufactured using a traditional manufacturing process; a flexible support is manufactured using a traditional manufacturing process T-shaped flexible member 25 in 2, and three hinges. The sealing key parts made by the micro-manufacturing process overcome the difficulty of the small displacement of the piezoelectric actuator 5, and can ensure that the valve body assembly 4 has good sealing performance and high control accuracy, and can reduce the valve body to a certain extent. The volume and quality of the body assembly 4; the flexible bracket 2 and the rest of the valve body assembly 4 made by tradition...
PUM
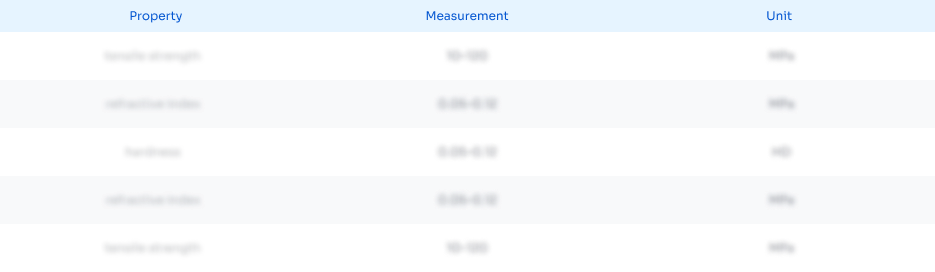
Abstract
Description
Claims
Application Information

- R&D Engineer
- R&D Manager
- IP Professional
- Industry Leading Data Capabilities
- Powerful AI technology
- Patent DNA Extraction
Browse by: Latest US Patents, China's latest patents, Technical Efficacy Thesaurus, Application Domain, Technology Topic, Popular Technical Reports.
© 2024 PatSnap. All rights reserved.Legal|Privacy policy|Modern Slavery Act Transparency Statement|Sitemap|About US| Contact US: help@patsnap.com