Composite structure of radiator fan and molding method thereof
A heat dissipation fan and combined structure technology, applied in the direction of cooling/ventilation/heating transformation, non-variable pumps, pump devices, etc., can solve problems such as poor smoothness, high difficulty in implementing precise positioning, and high noise, and achieve Combined positioning accuracy improvement effect
- Summary
- Abstract
- Description
- Claims
- Application Information
AI Technical Summary
Problems solved by technology
Method used
Image
Examples
Embodiment
[0025] Example: see attached figure 1 , 2 As shown, the combined structure of the cooling fan includes:
[0026] A base plate 10, which can be a metal plate body, includes a mounting surface 11 and a stator installation surface 12, and a circuit board 13 is arranged on the stator installation surface 12;
[0027] A stator nest positioning part 14 is provided at the center of the stator mounting surface 12 of the base plate 10;
[0028] A stator group 20, including a plurality of silicon steel sheets 21, coils 22 and a plastic insulating frame 23, the plastic insulating frame 23 wraps the silicon steel sheet 21 to shape;
[0029] A plastic composite seat 30 integrally formed on the stator group 20, the plastic composite seat 30 is integrally protruded from the center of the plastic insulating frame 23 of the stator group 20, and the shape of the plastic composite seat 30 can be The sub-seat positioning part 14 is set in the center of the stator installation surface 12 of the...
PUM
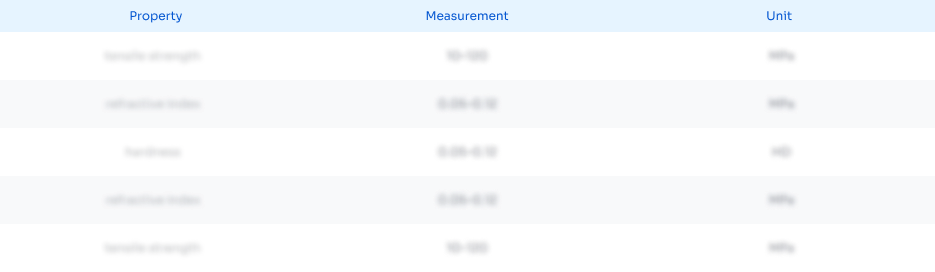
Abstract
Description
Claims
Application Information

- Generate Ideas
- Intellectual Property
- Life Sciences
- Materials
- Tech Scout
- Unparalleled Data Quality
- Higher Quality Content
- 60% Fewer Hallucinations
Browse by: Latest US Patents, China's latest patents, Technical Efficacy Thesaurus, Application Domain, Technology Topic, Popular Technical Reports.
© 2025 PatSnap. All rights reserved.Legal|Privacy policy|Modern Slavery Act Transparency Statement|Sitemap|About US| Contact US: help@patsnap.com