Gas spindle
An air-floating spindle and spindle technology, which is applied to bearings, shafts, bearings, instruments, etc., can solve the problems of insufficient air-floating force, unstable air source, and limit the load capacity of objects, so as to expand the weight range and improve reliability. Effect
- Summary
- Abstract
- Description
- Claims
- Application Information
AI Technical Summary
Problems solved by technology
Method used
Image
Examples
Embodiment 1
[0015] This embodiment is a large-load air bearing spindle applied to the Y901200D large-load roundness-waviness instrument. Including main shaft 6, upper end cover plate 2, lower end cover plate 8 and shaft sleeve parts.
[0016] Both ends of the main shaft 6 are connected with an upper end cover 2 and a lower end cover 8 . A shaft sleeve composed of an outer sleeve 4 and an inner sleeve 5 is fitted on the main shaft 6, and the main shaft and the shaft sleeve are loosely fitted. The loading platform 1 is located above the upper end plate 2 and is fixedly connected with the upper surface of the upper end plate 2 . The lower end of the main shaft part is connected with the motor. There is an air passage connected between the outer jacket 4 and the inner sleeve 5, and the arrangement of the air passage adopts the prior art. A nozzle 7 is embedded at the end of each gas path.
[0017] Such as figure 1 As shown, there are two groups of annular uniformly distributed nozzles 7 ...
Embodiment 2
[0021] This embodiment is applied to the air bearing spindle of the Y9030D roundness-waviness instrument. Including main shaft 6, upper end cover plate 2, lower end cover plate 8 and shaft sleeve parts.
[0022] Both ends of the main shaft 6 are connected with an upper end cover 2 and a lower end cover 8 . A shaft sleeve composed of an outer sleeve 4 and an inner sleeve 5 is fitted on the main shaft 6, and the main shaft and the shaft sleeve are loosely fitted. The loading platform 1 is located above the upper end plate 2 and is fixedly connected with the upper surface of the upper end plate 2 . The lower end of the main shaft part is connected with the motor. There is an air passage connected between the outer jacket 4 and the inner sleeve 5, and the arrangement of the air passage adopts the prior art. A nozzle 7 is embedded at the end of each gas path.
[0023] Such as figure 1 As shown, there are two groups of annular uniformly distributed nozzles 7 on both ends of the...
Embodiment 3
[0027] This embodiment is applied to the air bearing spindle of the DY300 cylindricity measuring instrument. Including main shaft 6, upper end cover plate 2, lower end cover plate 8 and shaft sleeve parts.
[0028] Both ends of the main shaft 6 are connected with an upper end cover 2 and a lower end cover 8 . A shaft sleeve composed of an outer sleeve 4 and an inner sleeve 5 is fitted on the main shaft 6, and the main shaft and the shaft sleeve are loosely fitted. The loading platform 1 is located above the upper end plate 2 and is fixedly connected with the upper surface of the upper end plate 2 . The lower end of the main shaft part is connected with the motor. There is an air passage connected between the outer jacket 4 and the inner sleeve 5, and the arrangement of the air passage adopts the prior art. A nozzle 7 is embedded at the end of each gas path.
[0029] Such as figure 1 As shown, there are two groups of annular uniformly distributed nozzles 7 on both ends of ...
PUM
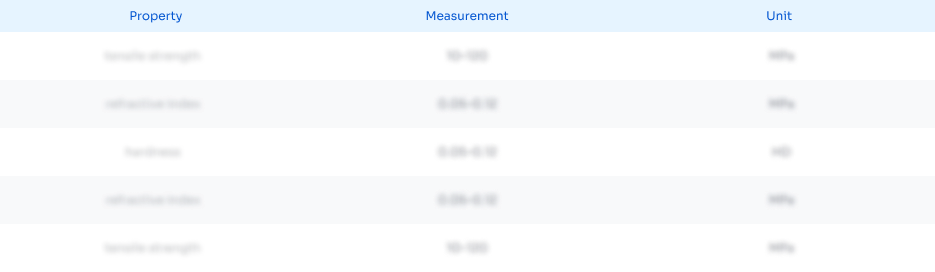
Abstract
Description
Claims
Application Information

- R&D
- Intellectual Property
- Life Sciences
- Materials
- Tech Scout
- Unparalleled Data Quality
- Higher Quality Content
- 60% Fewer Hallucinations
Browse by: Latest US Patents, China's latest patents, Technical Efficacy Thesaurus, Application Domain, Technology Topic, Popular Technical Reports.
© 2025 PatSnap. All rights reserved.Legal|Privacy policy|Modern Slavery Act Transparency Statement|Sitemap|About US| Contact US: help@patsnap.com