Isothermal spheroidizing annealing furnace for bearing steels
A technology of isothermal spheroidization and bearing steel, applied in furnaces, furnace components, indirect carbon dioxide emission reduction, etc., can solve problems such as waste of heat energy, environmental pollution, waste of heat energy
- Summary
- Abstract
- Description
- Claims
- Application Information
AI Technical Summary
Problems solved by technology
Method used
Image
Examples
Embodiment Construction
[0011] The present invention will be further described below in conjunction with the accompanying drawings.
[0012] see figure 1 As shown, the bearing steel isothermal spheroidizing annealing furnace includes a furnace body 1 with a furnace mouth 2 at the front and rear ends, and the furnace body 1 has a furnace 3 connected with the furnace mouth 2 at the front and rear ends. The furnace port 2 enters the furnace chamber 3, and after annealing treatment, it is output from the furnace port 2 at the other end. figure 1 In the above, the left side of the observer is defined as the front, and the right side is defined as the rear, and the upper and lower two-layer drive roller sets 4 and 5 for horizontally conveying the bearing steel between the furnace mouths 2 at the front and rear ends are arranged in the furnace 3, The upper and lower material roller tables 6 and 7 are arranged in front of the furnace mouth 2 at the front end of the furnace body 1 and behind the furnace mout...
PUM
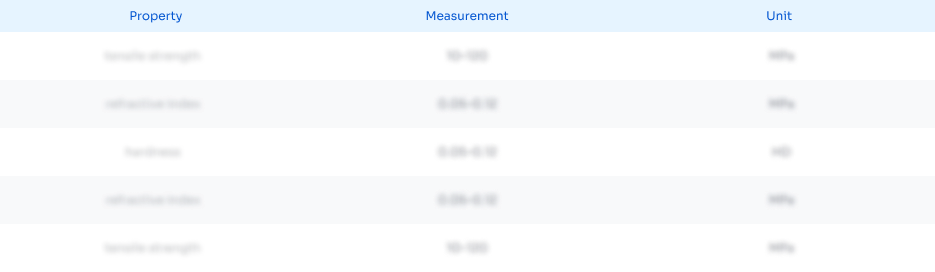
Abstract
Description
Claims
Application Information

- R&D
- Intellectual Property
- Life Sciences
- Materials
- Tech Scout
- Unparalleled Data Quality
- Higher Quality Content
- 60% Fewer Hallucinations
Browse by: Latest US Patents, China's latest patents, Technical Efficacy Thesaurus, Application Domain, Technology Topic, Popular Technical Reports.
© 2025 PatSnap. All rights reserved.Legal|Privacy policy|Modern Slavery Act Transparency Statement|Sitemap|About US| Contact US: help@patsnap.com