Method for producing woven weftwise hollow fabric
A production method and technology in the weft direction, applied in the direction of fabrics, embossed fabrics, and embossed fabrics, etc., to achieve the effects of reducing dosage, improving air permeability, and reducing processing pressure
- Summary
- Abstract
- Description
- Claims
- Application Information
AI Technical Summary
Problems solved by technology
Method used
Image
Examples
Embodiment 1
[0021] Example 1: In Figure 1-5 In the shown example 1, the processes of gray cloth weaving, gray cloth washing, singeing and desizing, scouring and bleaching, caustic soda mercerizing, whitening, tentering and pre-shrinking are sequentially carried out, wherein, in the gray cloth weaving process, the fabric warp yarn The thread is made of 11.7 tex pure cotton yarn, the weft direction is made of 14.6 tex pure cotton yarn marked with a and the vinylon filament of 50 denier is marked with b. The weft arrangement is 18a2b, that is, the loom introduces 18 pure cotton yarns and 2 vinylon filaments sequentially during the weft insertion movement, and then introduces them sequentially; in the gray cloth washing process, the washing temperature is 90 ° C; singeing In the desizing process, the washing temperature is 95°C; in the scouring and bleaching process, the washing temperature is 95°C; in the caustic soda mercerizing process, the concentration of caustic soda is 211g / l, and the...
Embodiment 2
[0022] Example 2: In Figure 6-10 In the shown embodiment 2, the processes of gray cloth weaving, gray cloth washing, singeing and desizing, scouring and bleaching, caustic soda mercerizing, dyeing, tentering and pre-shrinking are sequentially carried out, wherein, in the gray cloth weaving process, the fabric warp yarn Use 14.6 tex pure cotton yarn, weft use 14.6 tex pure cotton yarn with a mark and 50 denier vinylon filament with b mark. The weft arrangement is 48a2b10a2b10a2b10a2b48a2b, that is, the loom sequentially introduces 48 pure cotton yarns, 2 vinylon filaments, 10 pure cotton yarns, 2 vinylon filaments, and 10 pure cotton yarns during the weft insertion movement. Thread, 5 vinylon filaments, 10 pure cotton yarns, 5 vinylon filaments, 48 pure cotton yarns, and 2 vinylon filaments; they will be introduced in sequence in turn; in the gray cloth washing process, the washing temperature is 90°C; In the singeing and desizing process, the washing temperature is 95°C. I...
PUM
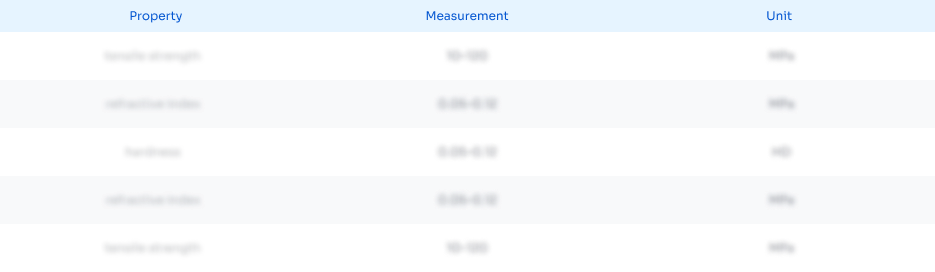
Abstract
Description
Claims
Application Information

- R&D
- Intellectual Property
- Life Sciences
- Materials
- Tech Scout
- Unparalleled Data Quality
- Higher Quality Content
- 60% Fewer Hallucinations
Browse by: Latest US Patents, China's latest patents, Technical Efficacy Thesaurus, Application Domain, Technology Topic, Popular Technical Reports.
© 2025 PatSnap. All rights reserved.Legal|Privacy policy|Modern Slavery Act Transparency Statement|Sitemap|About US| Contact US: help@patsnap.com