Method for operating workplaces on a textile machine for creating cross-wound spools
A technology for cross-winding bobbins and textile machines, which is used in thin material handling, conveying filamentous materials, transportation and packaging, etc., to achieve the effect of reliable rotation
- Summary
- Abstract
- Description
- Claims
- Application Information
AI Technical Summary
Problems solved by technology
Method used
Image
Examples
Embodiment Construction
[0024] figure 1 A side view of a station 2 of a textile machine 1 (in this embodiment a so-called automatic cross-winder) for producing cross-wound bobbins is schematically shown. As is known, automatic cross-winders 1 of this type all have a large number of identically constructed stations 2 between their end frames (not shown). The worsted bobbin 3 produced on the ring spinning machine is rewound at these stations 2 to form a high-capacity cross-wound bobbin 5 which, after it has been completed, is passed through a service assembly (not shown). out), such as a cross-wound bobbin doffer, is transported along the length of the machine to the cross-wound bobbin transfer mechanism 7 and to a bobbin loading station arranged at the end of the machine, etc., as is known, Therefore no more detailed description will be given. Automatic cross-winders 1 of this type usually also have a logistics mechanism in the form of a bobbin and tube transport system 6 , in which the worsted bobb...
PUM
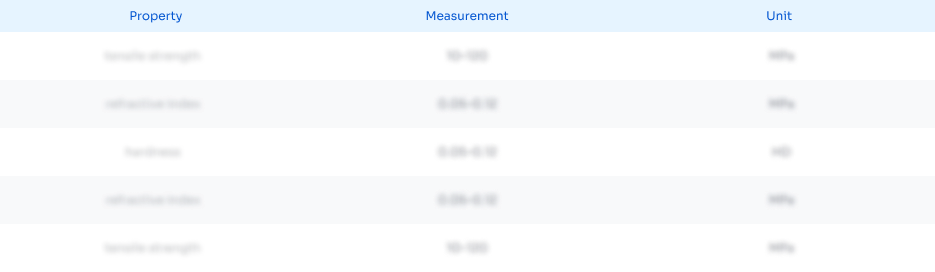
Abstract
Description
Claims
Application Information

- R&D Engineer
- R&D Manager
- IP Professional
- Industry Leading Data Capabilities
- Powerful AI technology
- Patent DNA Extraction
Browse by: Latest US Patents, China's latest patents, Technical Efficacy Thesaurus, Application Domain, Technology Topic, Popular Technical Reports.
© 2024 PatSnap. All rights reserved.Legal|Privacy policy|Modern Slavery Act Transparency Statement|Sitemap|About US| Contact US: help@patsnap.com