Method for improving crushing vibrating screening efficiency
A vibrating screening and vibrating screen technology, applied in chemical instruments and methods, filter screens, solid separation, etc., can solve the problems of difficult operation, high center of gravity of vibrating screens, and many machine failures, etc. The effect of slope height and improving screening efficiency
- Summary
- Abstract
- Description
- Claims
- Application Information
AI Technical Summary
Problems solved by technology
Method used
Examples
Embodiment Construction
[0015] The screen materials include metal woven net, wear-resistant rubber screen and polyurethane screen. The experiment shows that the life of the screen increases in turn, the opening ratio decreases in turn, the screening efficiency decreases in turn, and the weight of the screen decreases in turn. Passing ability decreases in turn. The screen material of the linear vibrating screen is improved to polyurethane screen.
[0016] What kind of sieve hole to choose mainly depends on the requirements for the particle size of the sieved product and the use of the under-sieved product. Compared with sieve holes of other shapes, under the condition of the same nominal size, the particle size of the undersize material passing through the linear sieve hole is smaller. For example, the maximum particle size of the particles passing through the 80%--85% of the size of the square mesh particles. The particle size passing through the rectangular sieve hole is larger than the material p...
PUM
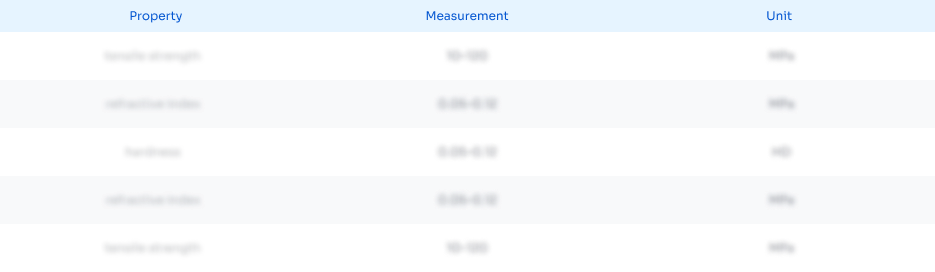
Abstract
Description
Claims
Application Information

- R&D
- Intellectual Property
- Life Sciences
- Materials
- Tech Scout
- Unparalleled Data Quality
- Higher Quality Content
- 60% Fewer Hallucinations
Browse by: Latest US Patents, China's latest patents, Technical Efficacy Thesaurus, Application Domain, Technology Topic, Popular Technical Reports.
© 2025 PatSnap. All rights reserved.Legal|Privacy policy|Modern Slavery Act Transparency Statement|Sitemap|About US| Contact US: help@patsnap.com