Base, film forming device and film forming method
A technology of a film forming device and a film forming method, which is applied to gaseous chemical plating, coatings, electrical components, etc., can solve the problems of uneven temperature distribution, uneven thickness of epitaxial film, damage or slip of base 302, etc.
- Summary
- Abstract
- Description
- Claims
- Application Information
AI Technical Summary
Problems solved by technology
Method used
Image
Examples
Embodiment Construction
[0028] figure 1 It is a schematic cross-sectional view of the sheet-fed film-forming apparatus 100 of this embodiment.
[0029] In this embodiment, a silicon wafer 101 is used as a substrate. However, it is not limited thereto, and wafers made of other materials may also be used depending on circumstances.
[0030] The film forming apparatus 100 has a chamber 103 as a film forming chamber.
[0031] The upper part of the chamber 103 is provided with a gas supply unit 123 for supplying source gases for forming a crystal film on the surface of the heated silicon wafer 101 . Furthermore, a shower plate 124 having a plurality of discharge holes for raw material gas is connected to the gas supply unit 123 . By arranging the shower plate 124 to face the surface of the silicon wafer 101 , the source gas can be supplied to the surface of the silicon wafer 101 .
[0032] A plurality of gas exhaust units 125 are provided at the lower part of the chamber 103 for exhausting the reacte...
PUM
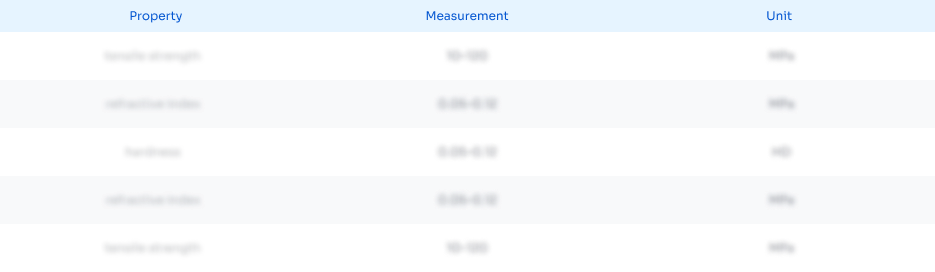
Abstract
Description
Claims
Application Information

- Generate Ideas
- Intellectual Property
- Life Sciences
- Materials
- Tech Scout
- Unparalleled Data Quality
- Higher Quality Content
- 60% Fewer Hallucinations
Browse by: Latest US Patents, China's latest patents, Technical Efficacy Thesaurus, Application Domain, Technology Topic, Popular Technical Reports.
© 2025 PatSnap. All rights reserved.Legal|Privacy policy|Modern Slavery Act Transparency Statement|Sitemap|About US| Contact US: help@patsnap.com