Composite self-lubricating bearing
A self-lubricating bearing and composite technology, applied in the direction of bearings, bearing components, shafts and bearings, etc., can solve the problems of self-lubricating bearing capacity limitation, difficult oil supply, self-lubricating bearing wear, etc., to meet the needs of industrial applications , Flexible design and application, the effect of extending the limit of use
- Summary
- Abstract
- Description
- Claims
- Application Information
AI Technical Summary
Problems solved by technology
Method used
Image
Examples
Embodiment Construction
[0020] The above and other technical features and advantages of the present invention will be described in more detail below in conjunction with the accompanying drawings.
[0021] Refer to the following Figure 1 to Figure 8 , to further illustrate the composite self-lubricating bearing of the present invention.
[0022] see Figure 1 to Figure 5 As shown, they are the three-dimensional appearance view, three-dimensional exploded view, bearing unit combination schematic diagram, assembly sectional view and assembly sectional view of the shaft core assembly of the first embodiment of the present invention; the composite self-lubricating bearing is composed of a housing 1 and The bearing set consists of 2, of which:
[0023] The housing 1 is a hollow cylinder penetrating in the axial direction to form an accommodating space 10, which is made of dense solid material or porous material, and the inner wall of the accommodating space 10 is provided with Extending at least one ri...
PUM
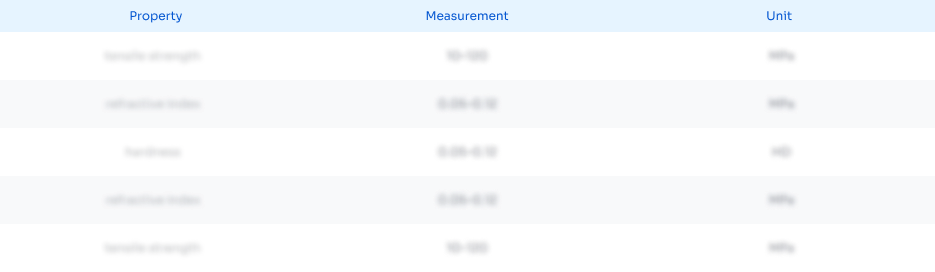
Abstract
Description
Claims
Application Information

- R&D
- Intellectual Property
- Life Sciences
- Materials
- Tech Scout
- Unparalleled Data Quality
- Higher Quality Content
- 60% Fewer Hallucinations
Browse by: Latest US Patents, China's latest patents, Technical Efficacy Thesaurus, Application Domain, Technology Topic, Popular Technical Reports.
© 2025 PatSnap. All rights reserved.Legal|Privacy policy|Modern Slavery Act Transparency Statement|Sitemap|About US| Contact US: help@patsnap.com